The Future Of Construction Technology: 4 Trends To Watch In 2024
The construction industry is experiencing rapid technological advancements, reshaping how projects are designed, managed, and executed.
The construction industry is experiencing rapid technological advancements, reshaping how projects are designed, managed, and executed. Construction professionals must understand the emerging technologies that will enhance efficiency and sustainability. Here are some key construction technology trends and innovations shaping its future.
1. Sustainable Construction Practices
Sustainability continues to be a driving force in the construction industry. In 2024, expect to see an increased focus on eco-friendly materials and methods. Companies are prioritizing the use of recycled materials, energy-efficient building systems, and designs that minimize environmental impact. Our marketplace supports this trend by offering a wide range of sustainable bulk materials, ensuring that your projects meet regulatory requirements and contribute to a greener future.
2. Advanced Building Information Modeling
Building Information Modeling (BIM) has been a game-changer for the construction industry, and its capabilities are expanding. In 2024, BIM will become even more integral to project planning and execution. Enhanced 4D and 5D BIM tools will allow for better visualization of project timelines and cost management, leading to more accurate forecasting and resource allocation. Our platform integrates seamlessly with BIM systems, providing real-time data on material availability and pricing.
3. Artificial Intelligence and Machine Learning
Artificial Intelligence (AI) and machine learning (ML) are set to revolutionize construction management. These technologies can analyze vast amounts of data to predict project outcomes, optimize workflows, and identify potential risks before they become issues. For instance, predictive analytics can help plan material orders, reduce waste, and ensure timely delivery.
AI and ML will also play a crucial role in enhancing safety on construction sites. Advanced analytics can identify patterns and trends in safety data, allowing companies to implement targeted interventions to reduce accidents. Additionally, AI-powered surveillance systems can monitor construction sites in real time, detecting hazardous conditions and alerting workers immediately.
Our marketplace leverages AI to provide intelligent recommendations and insights, making your procurement process smarter and more efficient.
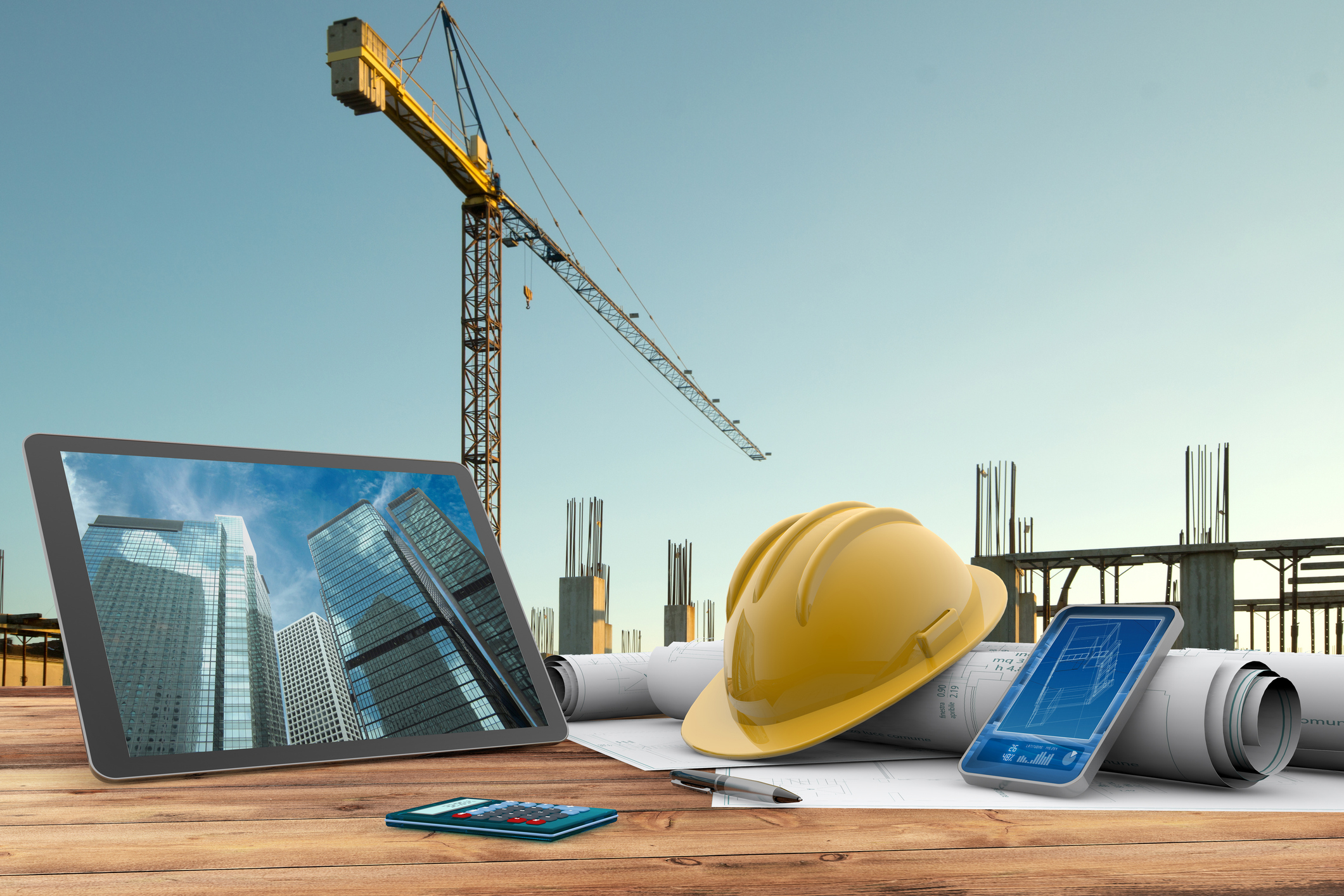
4. Autonomous Construction Equipment
Robotics and automation are transforming construction sites into hubs of efficiency and precision. Autonomous construction equipment such as drones, bulldozers, and excavators will become more prevalent. These machines can perform tasks like site surveying, earthmoving, and material handling with minimal human intervention, reducing labor costs and increasing productivity.
The future of construction technology brings numerous advancements to the industry that will transform how projects are designed, managed, and executed. From BIM enhancements and robotics to sustainable practices and AI-powered solutions, construction professionals have many tools to improve efficiency, safety, and sustainability. As these technologies continue to evolve, staying informed and adapting to the latest trends will be crucial for success in the competitive construction industry. Embrace the future of construction technology, and position yourself at the forefront of innovation. Learn more about how we can help you!
Related Articles
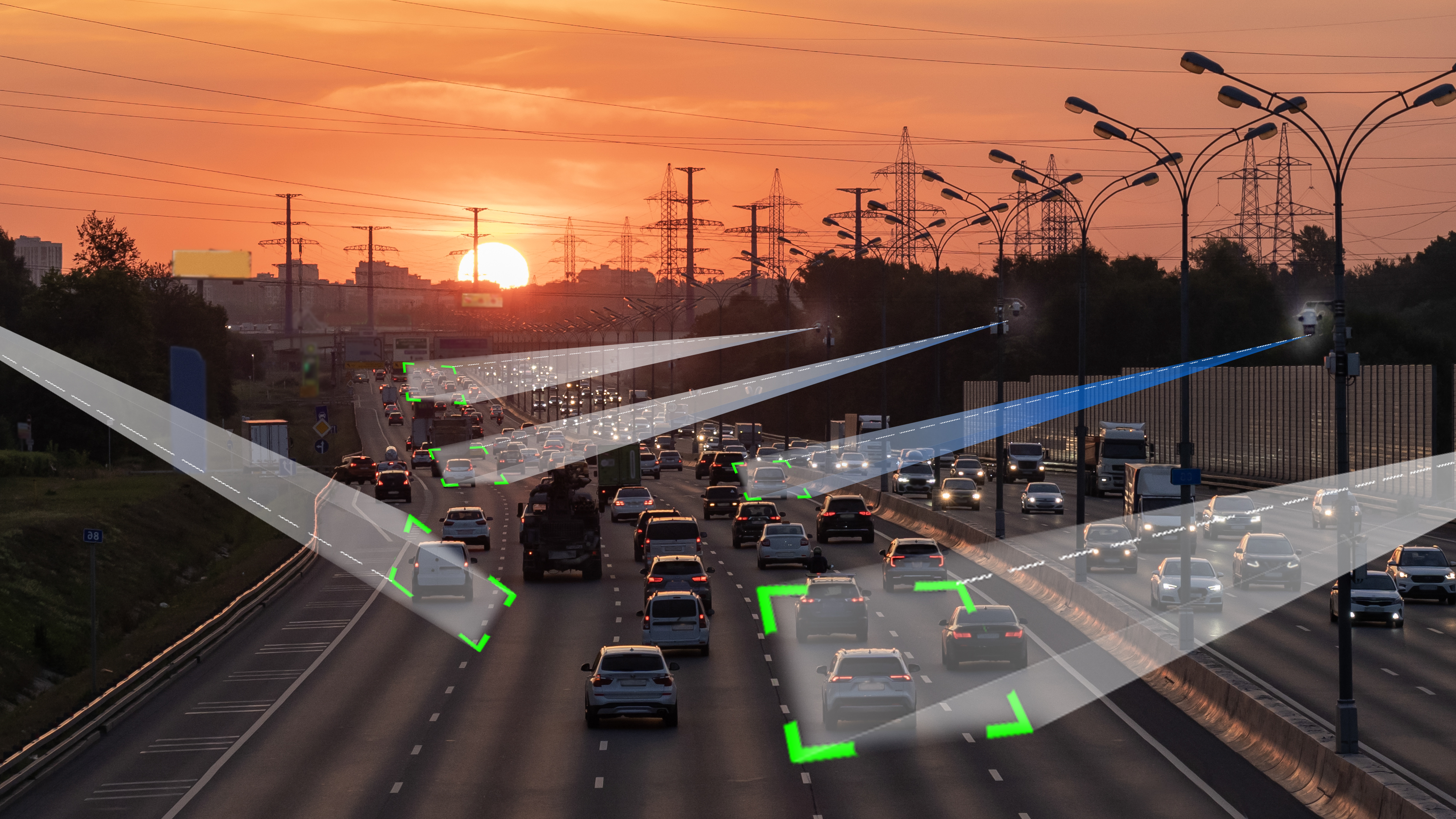
Top 5 Road Construction Innovations You Need to Know
The road construction industry is experiencing significant change. New road technologies and creative methods are changing how we build, maintain, and manage our roads. These improvements, such as environmentally friendly materials in road construction and equipment powered by artificial intelligence (AI), are making our road systems safer, more sustainable, and cost-effective.
As professionals in the construction field, it's crucial for us to stay updated on these new developments. It's not just an advantage anymore; it's necessary to survive in this competitive market. Modern contractors must adopt new technologies like digital quoting software and intelligent construction equipment to stay ahead and provide better results.
In this article, we will discuss five groundbreaking innovations that are raising the bar in road construction:
- Sustainable pavement solutions
- Smart technology integration
- Advanced safety features
- Revolutionary construction materials
- Digital project management tools
These innovations are changing how we construct roads and reshaping the entire construction industry. Whether you're an experienced contractor or just starting, understanding these advancements will empower you to make wise choices for your upcoming projects.
1. Eco-Friendly Pavements
The rise of eco-friendly pavements marks a significant shift in road construction practices. These innovative surfaces combine environmental benefits with practical advantages, creating sustainable infrastructure solutions for modern cities.
Water-Saving Benefits
- Porous asphalt reduces water waste by allowing up to 80% of rainfall to seep through
- Natural groundwater replenishment occurs through filtered percolation
- Decreased need for irrigation in surrounding landscapes
Stormwater Management
- Pervious concrete acts as a natural filtration system
- Reduces puddle formation and hydroplaning risks
- Minimizes the strain on traditional drainage systems
- Helps prevent flash flooding in urban areas
The durability of eco-friendly pavements extends beyond environmental advantages. These materials demonstrate remarkable resilience:
- 20-30% longer lifespan compared to traditional pavements
- Reduced crack formation due to flexible composition
- Lower maintenance requirements save both time and resources
- Natural temperature regulation reduces heat island effects
The cost-effectiveness of these pavements becomes apparent through:
- Decreased need for regular repairs
- Reduced stormwater infrastructure requirements
- Lower long-term maintenance expenses
- Extended service life of the road surface
These innovative pavement solutions, such as permeable pavements, represent a practical approach to sustainable infrastructure, balancing environmental responsibility with economic efficiency. Integrating these materials into road construction projects creates lasting positive impacts for communities and ecosystems alike. For instance, sustainable paving practices enhance the durability and functionality of roads and significantly contribute to environmental conservation efforts.
2. Advanced Smart Technology in Road Construction
The construction industry is going through a digital transformation, with innovative technologies changing how road construction has traditionally been done. These new developments bring unmatched accuracy, safety, and efficiency to job sites.
AI-Powered Equipment
Some examples of AI-powered equipment used in road construction include:
- Autonomous vehicles and machinery equipped with sensors
- Real-time monitoring of equipment performance
- Predictive maintenance scheduling
- Automated grading and paving systems
Through integrated platforms, smart technologies enable seamless communication between workers, machines, and project managers.
Construction teams can now:
- Share real-time updates
- Access digital blueprints instantly
- Track progress through mobile apps
- Coordinate multiple tasks simultaneously
Robotics Revolution
The integration of robotics in road construction has dramatically improved productivity:
- Automated pavers achieve perfect precision
- Robotic flaggers enhance worker safety
- Drones survey sites and monitor progress
- 3D printing technology creates custom components
These smart systems collect valuable data throughout the construction process. Project managers use this information to:
- Optimize resource allocation
- Reduce equipment downtime
- Minimize material waste
- Improve project timelines
Cloud computing platforms enable teams to analyze this data and make informed decisions in real-time. The result? Faster project completion, reduced costs, and improved safety standards across construction sites.
Additionally, the adoption of smart technologies extends beyond AI and robotics, encompassing areas like IoT, big data analytics, and advanced materials, which collectively enhance the overall effectiveness and sustainability of road construction projects.
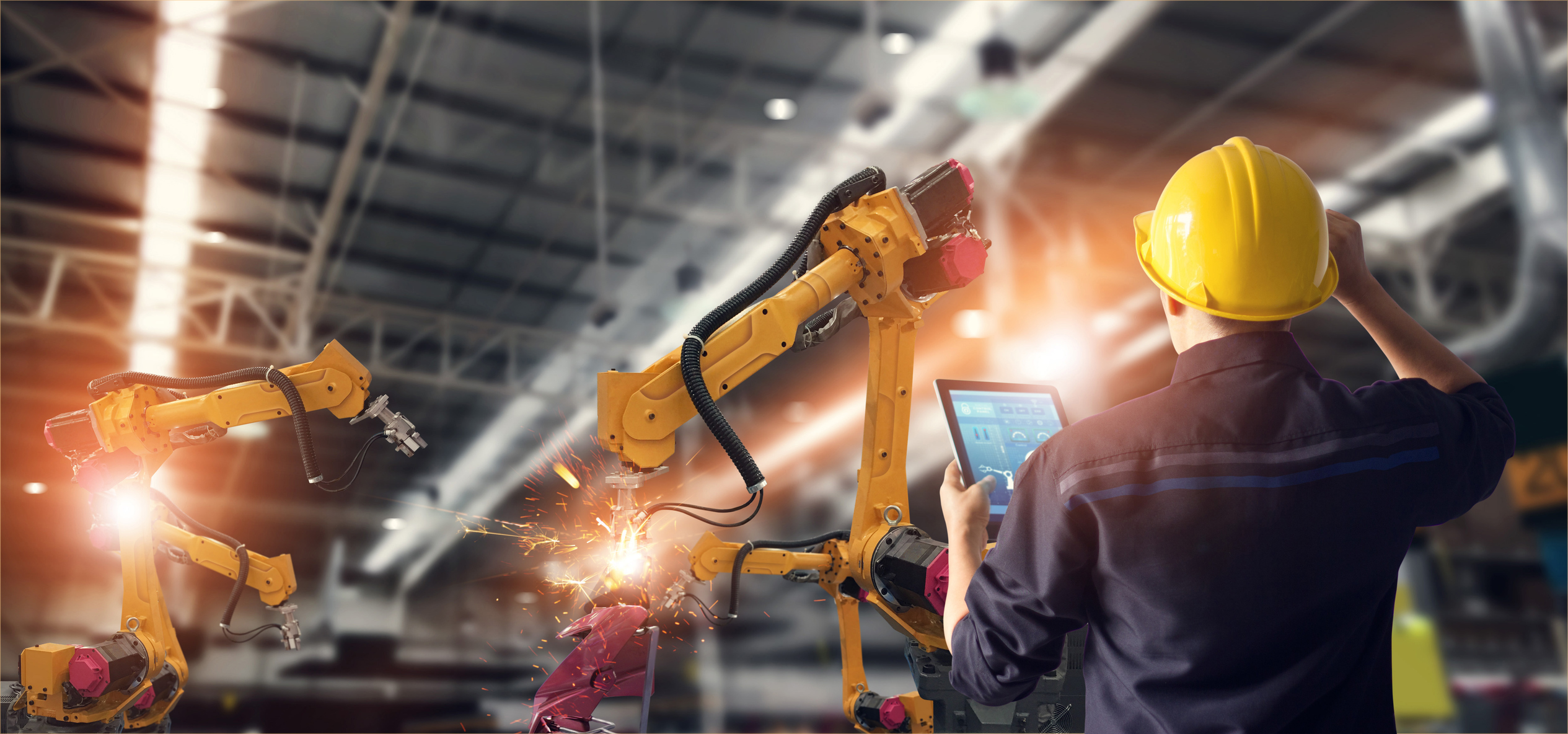
3. Improving Road Safety With Technology Innovations
Road safety innovations are transforming how we protect drivers and pedestrians through groundbreaking technologies and smart design solutions. These advancements create safer road environments while reducing accident rates. innovations in constructioninnovations in construction
Dynamic Paint and Glow-in-the-Dark Markings
- Temperature-sensitive paint changes color to warn drivers of icy conditions
- Photoluminescent road markings absorb daylight and illuminate at night
- Solar-powered LED markers provide enhanced visibility during adverse weather
Smart Safety Features
- Anti-icing road surfaces with embedded heating elements
- Self-healing materials that repair minor cracks before they become hazardous
- Acoustic barrier systems that reduce noise pollution and increase driver focus
Innovative Design Elements
- 3D crosswalks creating optical illusions to slow traffic
- Smart traffic signals adapting to real-time conditions
- Interactive warning systems detecting wrong-way drivers
These safety innovations in construction have shown promising results in pilot projects worldwide. The Netherlands' glow-in-the-dark highways reported a 70% reduction in nighttime accidents, while Seattle's anti-icing roads decreased winter accidents by 50%.
The integration of these safety features doesn't just protect lives - it creates a more efficient and sustainable road network. Cities implementing these technologies report significant reductions in maintenance costs and improved traffic flow during challenging weather conditions.
What Advanced Materials Are Used for Road Construction
The road construction industry is experiencing a materials revolution with groundbreaking innovations in asphalt mixtures. Plastic-infused asphalt stands out as a game-changing solution that tackles both infrastructure and environmental challenges.
This innovative material combines traditional asphalt with recycled plastic waste, creating a more durable road surface. Research shows plastic-modified roads can:
- Last up to 3 times longer than conventional roads
- Withstand extreme temperature variations
- Reduce the formation of potholes and cracks
- Support heavier traffic loads
The environmental impact is equally impressive. A one-kilometer stretch of plastic road can repurpose approximately 1 million plastic bags, reducing landfill waste and ocean pollution. The process of incorporating plastics into asphalt also:
- Decreases carbon emissions by 8% compared to traditional methods
- Reduces the need for virgin materials
- Minimizes construction waste
- Creates a circular economy for plastic waste
Several countries have successfully implemented plastic roads, with India leading the charge by mandating plastic waste in road construction. The Netherlands has installed bicycle paths using recycled plastic blocks, proving the versatility of these materials.
Sourcing these advanced materials has become easier through digital marketplaces specializing in bulk construction materials, making sustainable road building more accessible to contractors and municipalities.
5. Construction Data Integration in Road Projects
Digital transformation has changed the way road construction projects are managed. With the help of smart digital tools, tasks such as contractor bidding, material procurement, and project tracking can now be done more efficiently and with less effort.
Digital Project Management Tools
Some of the key digital tools being used in road projects include:
- Cloud-based collaboration platforms
- Real-time progress tracking
- Automated reporting systems
- Digital material procurement portals
- Instant communication channels
These tools not only save time but also reduce the chances of errors and miscommunication.
Smart Sensors for Traffic Management
The use of sensors in road construction has brought about a new level of accuracy in managing traffic and maintaining roads. These sensors have the capability to:
- Monitor traffic patterns
- Detect road surface conditions
- Alert maintenance crews to potential issues
- Optimize lane usage during peak hours
- Track environmental impacts
By having this real-time data, authorities can make informed decisions on how to improve traffic flow and maintain roads effectively.
AI-Powered Analytics for Contractors
Contractors can benefit greatly from the analysis of data using artificial intelligence (AI). With AI-powered analytics, they can:
- Predict when maintenance will be needed
- Allocate resources in the most efficient way possible
- Avoid delays in projects
- Reduce costs associated with operations
- Make better decisions based on data insights
This ability to anticipate problems and make proactive decisions can give contractors a competitive edge in the industry.
Simplified Material Sourcing with Digital Platforms
Finding and purchasing materials for construction projects can often be a time-consuming process. However, with the rise of digital procurement platforms, this process has become much simpler.
Contractors can now easily compare prices, check availability, and place orders through user-friendly interfaces. This not only saves time but also reduces administrative overhead costs.
Building Information Modeling (BIM) for Road Construction
Building Information Modeling (BIM) is becoming increasingly popular in road construction projects. It allows teams to create detailed 3D visualizations of their projects before any physical work begins.
By using BIM, teams can identify potential issues or conflicts that may arise during construction. This proactive approach leads to smoother execution and fewer costly mistakes down the line.
Conclusion
The road construction industry is on the brink of a technological revolution. From eco-friendly pavements that tackle environmental issues to smart technologies reshaping project execution, these innovations are laying the groundwork for future transportation.
Safety innovations like dynamic paint and glow-in-the-dark markings create safer roads for all users. Advanced materials, particularly plastic-infused asphalt, demonstrate how sustainability and durability can work hand in hand. The rise of digital tools and data-driven processes marks a new era in project management and maintenance prediction.
Ready to transform your road construction projects?
- Explore these innovative technologies
- Connect with industry experts
- Stay updated with the latest advancements
- Implement sustainable solutions
The future of road construction is here – embrace these innovations to build better, safer, and more sustainable roads. Visit Bulk Exchange to discover how you can integrate these groundbreaking solutions into your next project.
FAQs
What are eco-friendly pavements and how do they benefit road construction projects?
Eco-friendly pavements, such as porous asphalt and previous concrete, are innovative materials used in road construction that help save water by allowing stormwater to pass through. These pavements aid in managing stormwater runoff and preventing flooding, while also offering enhanced durability and reducing maintenance costs.
How smart technologies are transforming modern civil engineering highway construction
Smart technologies like robotics, artificial intelligence (AI), big data, and cloud computing are revolutionizing road construction by improving communication, safety, efficiency, and productivity. These advanced tools facilitate better project management and contribute to the adoption of innovative civil construction technology trends anticipated for 2025.
What safety innovations are being implemented in road design to enhance driver visibility?
Innovative safety systems for construction sites such as dynamic paint, glow-in-the-dark road markings, and anti-icing roads are being integrated into road designs. These technologies significantly improve visibility and safety for drivers, especially under challenging conditions, thereby reducing accidents and enhancing overall road safety.
How are advanced materials like recycled plastics influencing road building practices?
Advanced materials including recycled plastics infused into asphalt mixtures are transforming road construction by providing sustainable alternatives that reduce environmental impact. Utilizing these materials not only lowers carbon emissions but also supports sourcing bulk materials responsibly for infrastructure projects.
What role does digitization play in optimizing road project management?
Digitization introduces data-driven processes using sensors for vehicle guidance, digital tools for contractors, bidding software, and digital procurement systems. These technologies streamline project management, optimize lane capacity, predict maintenance needs, and enhance overall efficiency in road construction projects.
Why is it important for contractors to stay updated with the latest innovations in road construction?
Staying informed about the latest advancements—such as eco-friendly pavements, smart technologies, safety innovations, advanced materials, and digitization, is crucial for contractors to implement efficient, sustainable, and safe road projects. Embracing these innovations ensures competitiveness and aligns with future transportation trends and smart roads funding opportunities.
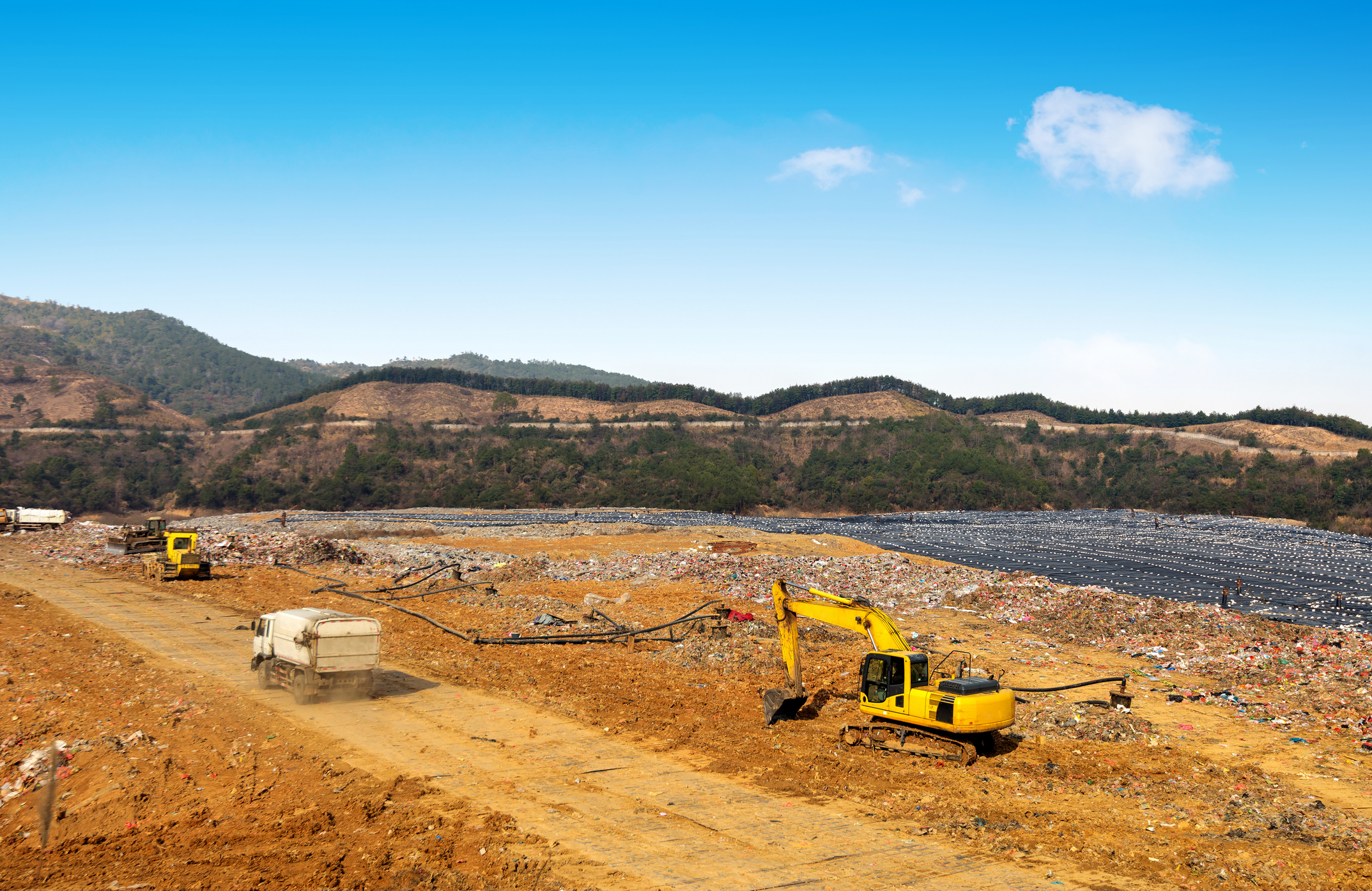
How to Know for Sure You’re Selecting the Best Local Supplier or Disposal Option
Choosing the right local supplier or disposal service will set your business up for success.
By Rachael Mahoney, Chief Strategist, Bulk Exchange
Everyone Has “Their Guy” But Is It Still Enough?
Ask any experienced estimator or planner you meet, and they’ll proudly swear they know every facility in their market. They’ve got their guy saved on speed dial, a trusted friend they can call for the “real” price, you know, the one reserved just for them because of years of mutual loyalty, help on late-night disasters, and (of course) rounds of golf and a few lively industry parties.
After decades of partnership, more than a few white-knuckle jobs where everything that could go wrong did, and the kind of relationships only this industry can foster, it would seem obvious you’re always getting the best deal and outcome… right?
We are in an industry where, for centuries, special relationships have been the secret sauce, the key to driving better margins, faster timelines, and fewer headaches. And they will absolutely continue to matter.
But…and this is a big but…compelling new tools and data are showing that sourcing materials and disposal services based only on relationships often leaves serious options, opportunities, and margin sitting on the table.
Especially now, as the industry is evolving at a pace that demands decisions rooted in analytics, not just vibes.
Why the Game is Changing: 4 Big Shifts You Can’t Ignore
1. The Great Retirement Is Coming
Over 70% of the gatekeepers of these valuable relationships are expected to retire in the next 5–7 years (according to construction industry workforce studies). The next generation of builders are digital natives who are growing up shopping and sourcing everything through technology. Handshakes and friendships will always matter, but they’ll be supplemented (and often outpaced) by smarter digital strategies.
2. Materials Are More Complex Than Ever
Sustainability initiatives, evolving material performance standards, and the rise of specialty mixes and engineered solutions mean material selection isn’t just about price or proximity anymore. It’s about understanding availability, environmental impact, and lifecycle performance, all of which require dynamic planning and immediate access to the right data.
3. Weight and Distance Now Matter Even More
When material scarcity hits during natural or manmade disasters, and trucking shortages persist, proximity becomes more than a nice-to-have, it becomes the deciding factor between profit and loss. Delivery logistics are now as critical as material pricing itself to achieving a successful project outcome.
4. Competition is Getting Fiercer (and Less Local)
As the market contracts and consolidates, every bid counts more. You’ll see more non-local competition, and new entrants won’t need the “good ol’ boy” network to lean on. Relationships will still help, but they won’t be the silver bullet they once were.
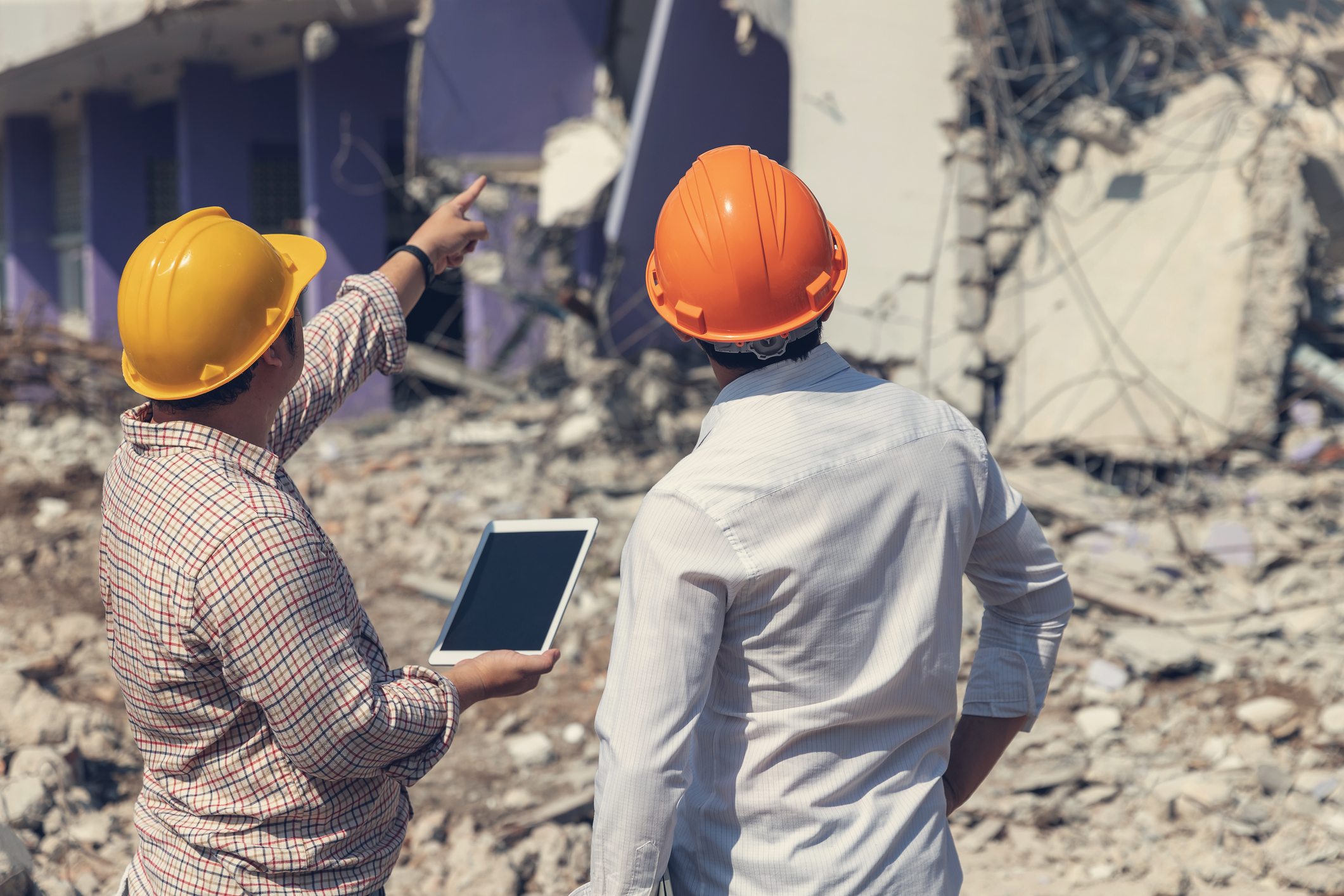
The Good News: The Well-Prepared Will Win
This isn’t a time to panic.
This is a time to prepare, to lean in, and to capture opportunity while many others freeze or try and wait it out.
Yes, we have been burned before by tech solutions that over-promise and under-deliver. Our industry knows firsthand how “solutions” that don’t understand the realities of heavy civil construction usually fail and fast.
But here’s the thing:
Entrepreneurship and innovation are made stronger by constructive failures. Every lesson from what didn’t work has paved the way for the solutions that now can, especially for those that pay attention and are willing to adjust.
What We’ve Learned and How We Built Bulk Exchange Differently
1. Deep Industry Expertise First
It starts at the top with our founder, Paul Foley, who’s spent his career, 30 years and across three continents, in heavy civil construction. From who we hire, to our loyal investors, we are deep on industry experience.
This industry isn’t just something we serve; it’s part of who we are. That experience ensures we build technology that respects construction’s unique DNA, using tools to enhance, not replace, the roots and relationships that built it.
2. Start Small, Solve Real Problems, Then Grow
Sure, construction is a multi-trillion-dollar industry. The temptation to “go big” immediately is real and it’s why so many ConTech startup’s fail.
We chose a different path:
Start with a specific, painful, solvable problem (material and disposal sourcing), nail it, and then scale thoughtfully from there.
3. Embrace the “We, Not Me” Mindset
Like our customers, collaboration is a core value at Bulk Exchange.
No one moves mountains (literally) or mega-projects alone.
We see ourselves as a true partner, working alongside the industry, not over it.
4. Prioritize Trust and Neutrality
Middlemen and brokers often thrive on secrecy.
We don’t.
Bulk Exchange is neutral, ALWAYS, and for good reason.
We exist to connect supply and demand transparently and level the playing field for everyone.
The Moral of the Story
Honor the roots. Respect the relationships. But embrace the tools that will future-proof your business.
The companies that will dominate this next era of construction won’t be the ones who cling stubbornly to old ways. They’ll be the ones who blend legacy with innovation, who recognize that a handshake and a smart sourcing platform aren’t enemies, they’re allies.
Because getting the best local supplier or disposal option today isn’t about who you know. It’s about what you know, and how fast you can act on it.
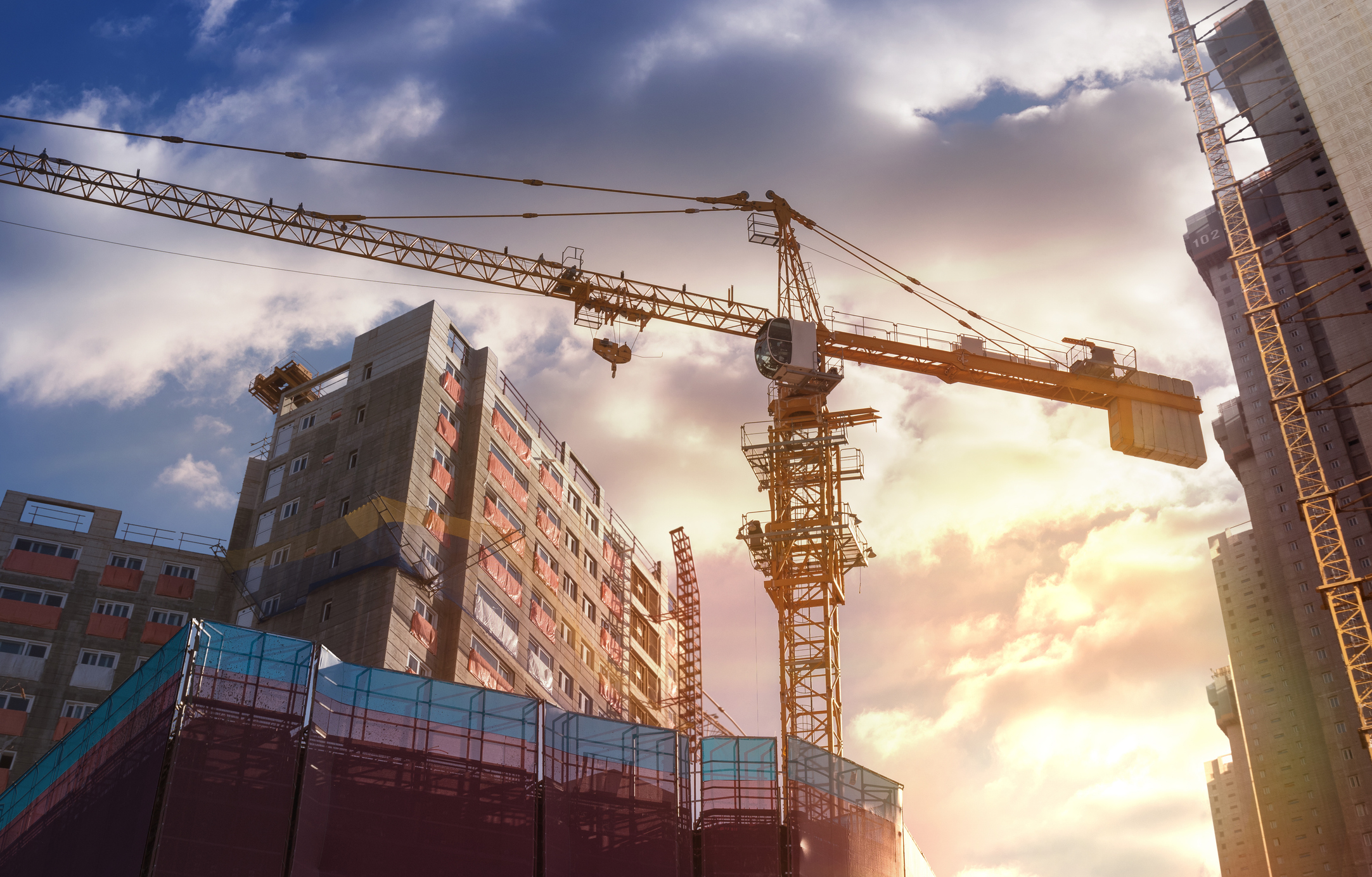
Redefining Value: From Life Choices to Construction Materials
In our daily lives, we constantly make value judgments. We assess the quality of experiences, relationships, and purchases based on certain criteria: durability, reliability, consistency, and long-term satisfaction rather than momentary pleasure. Yet when it comes to construction materials, the literal foundation of our built environment, we sometimes lose sight of these value metrics in favor of immediate cost savings.
The True Definition of Value
Value isn't simply about the lowest price point. True value encompasses performance, longevity, reliability, and increasingly, sustainability. Just as we wouldn't choose a friendship based solely on convenience, we shouldn't select construction materials based solely on acquisition cost.
"The construction materials industry is rapidly evolving beyond the outdated paradigm of choosing materials based on initial cost alone," says Michael Philipps, former President of the National Ready Mixed Concrete Association (NRMCA). "Today's definition of value must include resilience, sustainability, and total lifecycle performance. The cheapest option upfront often becomes the most expensive over time."
In the world of bulk construction materials, value manifests in specific, measurable ways:
Consistent gradation ensures predictable performance across batches. When aggregates maintain uniform size distribution, the resulting concrete or asphalt delivers reliable strength properties.
Cleanliness of materials prevents contamination that can compromise structural integrity. Foreign substances in aggregates can inhibit proper bonding and accelerate deterioration.
Durability translates directly to reduced maintenance costs and extended service life. Materials that resist weathering, abrasion, and chemical attack provide significantly greater long-term value.
Strength determines load-bearing capacity and resistance to failure. Higher-quality materials typically offer superior strength-to-weight ratios, enabling more efficient designs.
Adherence to ASTM and DOT specifications provides verified quality assurance. These standards represent industry consensus on minimum acceptable performance criteria, formed through rigorous testing and real-world experience.
"Quality aggregates are the backbone of resilient infrastructure," observes Karen Hubacz, Chairwoman of the National Stone, Sand & Gravel Association (NSSGA). "When we talk about extending the service life of our roads, bridges, and buildings, we're really talking about starting with materials that meet or exceed specifications. The difference between marginal materials and premium aggregates can mean decades of additional service life."
The Future of Value: Sustainability Meets Performance
The construction industry stands at a critical juncture. Climate change and resource scarcity demand that we reconsider how we define value in building materials. Fortunately, innovation is already providing solutions that harmonize performance with environmental responsibility.
Portland Limestone Cement (PLC) exemplifies this evolution in value. By replacing a portion of clinker with fine limestone, PLC reduces carbon emissions by 10% compared to traditional Portland cement while maintaining equivalent performance. This isn't just an environmental win—it's economically sound, as reducing clinker content lowers production energy requirements.
"PLC represents the kind of innovation that's transforming our industry," says Tom Beck, Executive Vice President of Summit Materials. "We're seeing materials that not only reduce environmental impact but actually outperform their traditional counterparts in many applications. This is the future of construction – where sustainability and superior performance go hand in hand."
Other innovations are rapidly transforming our options:
- Geopolymer concretes utilizing industrial byproducts like fly ash and slag
- Carbon-sequestering concrete that actually absorbs CO₂ during curing
- Mass timber products offering renewable alternatives to steel and concrete
- Recycled aggregate concrete reducing the need for virgin material extraction
"The asphalt industry has long been at the forefront of recycling and material innovation," notes Audrey Copeland, President and CEO of the National Asphalt Pavement Association (NAPA). "Today's high-performance asphalt mixes incorporate recycled materials while delivering longer-lasting, smoother, quieter roadways. This combination of sustainability and enhanced performance is redefining what value means in infrastructure construction."
The true breakthrough is that these sustainable alternatives aren't just "green options"—they're increasingly becoming the highest-performing, most economical choices. Much like LED lighting has surpassed incandescent bulbs in both performance and cost-efficiency, sustainable construction materials are poised to redefine value in the building industry.
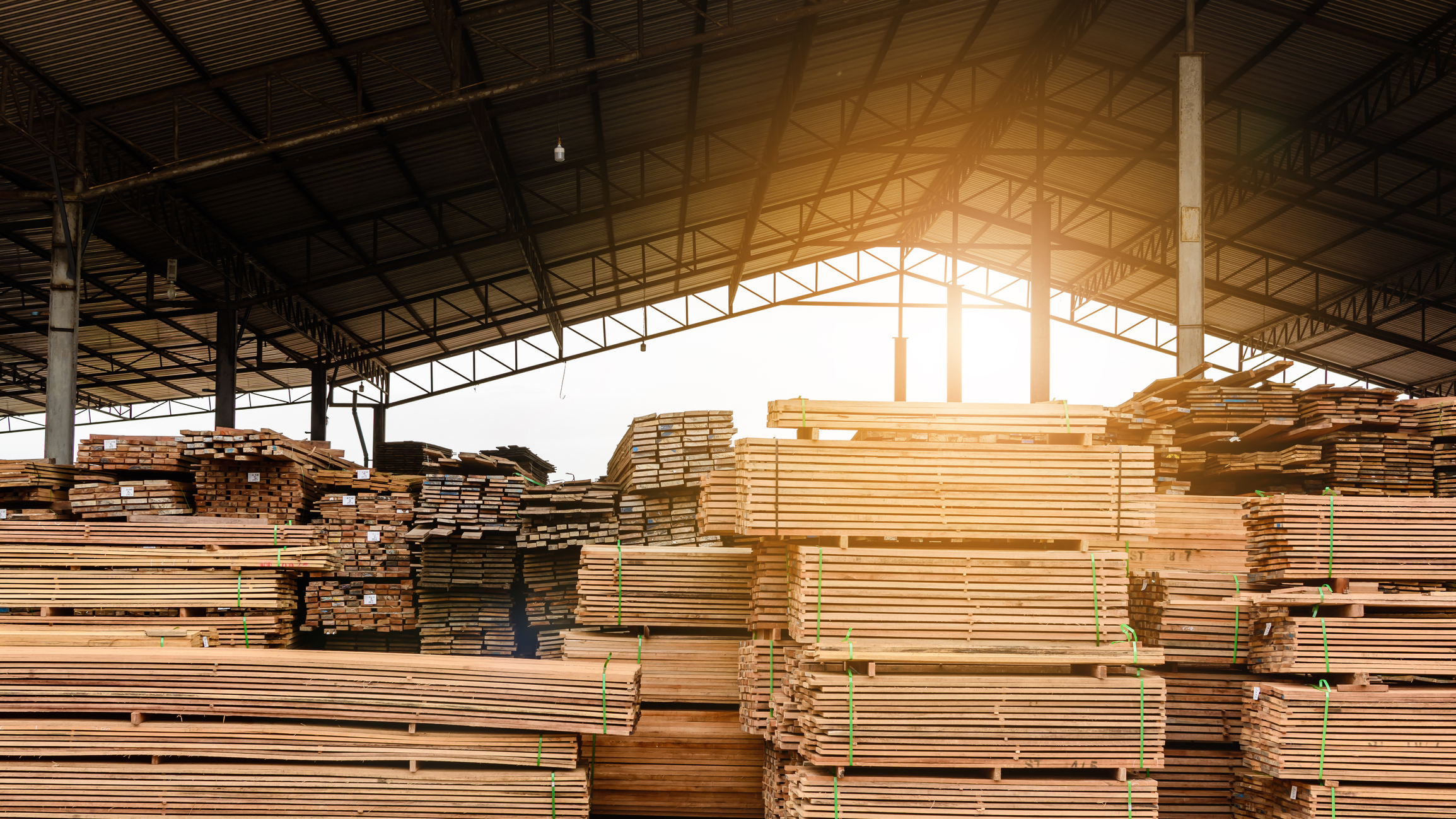
Overcoming the Knowledge Gap
The shift toward higher-value, sustainable materials faces one significant obstacle: awareness and access. Contractors, engineers, and project managers often default to familiar materials not because they prefer them, but because they lack information about alternatives and where to source them.
"One of our greatest challenges is connecting innovative products with the professionals who specify and use them," explains Rex Cottle, Executive Director, The National Steering Committee (NSC) - Concrete Industry Management (CIM). "We can develop the most sustainable, high-performance materials in the world, but they only create value when they're actually used in construction."
This knowledge gap represents perhaps the greatest barrier to adopting higher-value materials. How can professionals specify innovative products if they don't know these products exist or where to find them?
Bulk Exchange has emerged as the solution to this critical challenge. As the first and only complete directory of construction materials, Bulk Exchange enables professionals to discover, compare, and source next-generation materials in their local area. This platform bridges the information gap, making it easier than ever to select high-value materials for any project.
By providing comprehensive information on material properties, sustainability metrics, and local availability, Bulk Exchange empowers builders to make truly value-based decisions. The platform transforms the abstract concept of "better materials" into concrete actions: specifying PLC instead of traditional cement, selecting recycled concrete aggregate, or choosing locally-sourced materials to reduce transportation emissions.
The infrastructure we build today will serve communities for decades to come. By leveraging tools like Bulk Exchange to identify and source the highest-value materials, we're not just constructing buildings and bridges—we're creating a legacy of sustainability, performance, and true economic value. For the projects of tomorrow, choosing high-value materials isn't just preferable—it's essential. And now, with Bulk Exchange, it's also achievable.