Top Causes of Rework in Construction & How to Minimize It
Don't let rework slow down your construction projects! Learn the top causes of rework and how to prevent them.
Construction projects are complex and they involve many moving parts, tight deadlines, and significant investments. However, one thing can derail even the most well-planned project—rework. Rework is estimated to represent between 2% and 20% of total costs, according to the Construction Industry Institute (CII). This financial burden can be overwhelming, especially for firms operating on thin margins. Find out the top causes of construction rework and how you can minimize it on your projects.
1. Project Scope and Planning
Effective scope and planning are the backbone of any construction project. Poor planning often results in insufficient resources, causing delays and necessitating rework. Scheduling mishaps can also lead to overlap in tasks, which creates confusion and errors.
A solid project plan should include detailed timelines, stakeholders, budget, resource allocation, and contingency plans. This ensures that everyone knows their role and responsibilities, reducing the likelihood of mistakes that lead to rework.
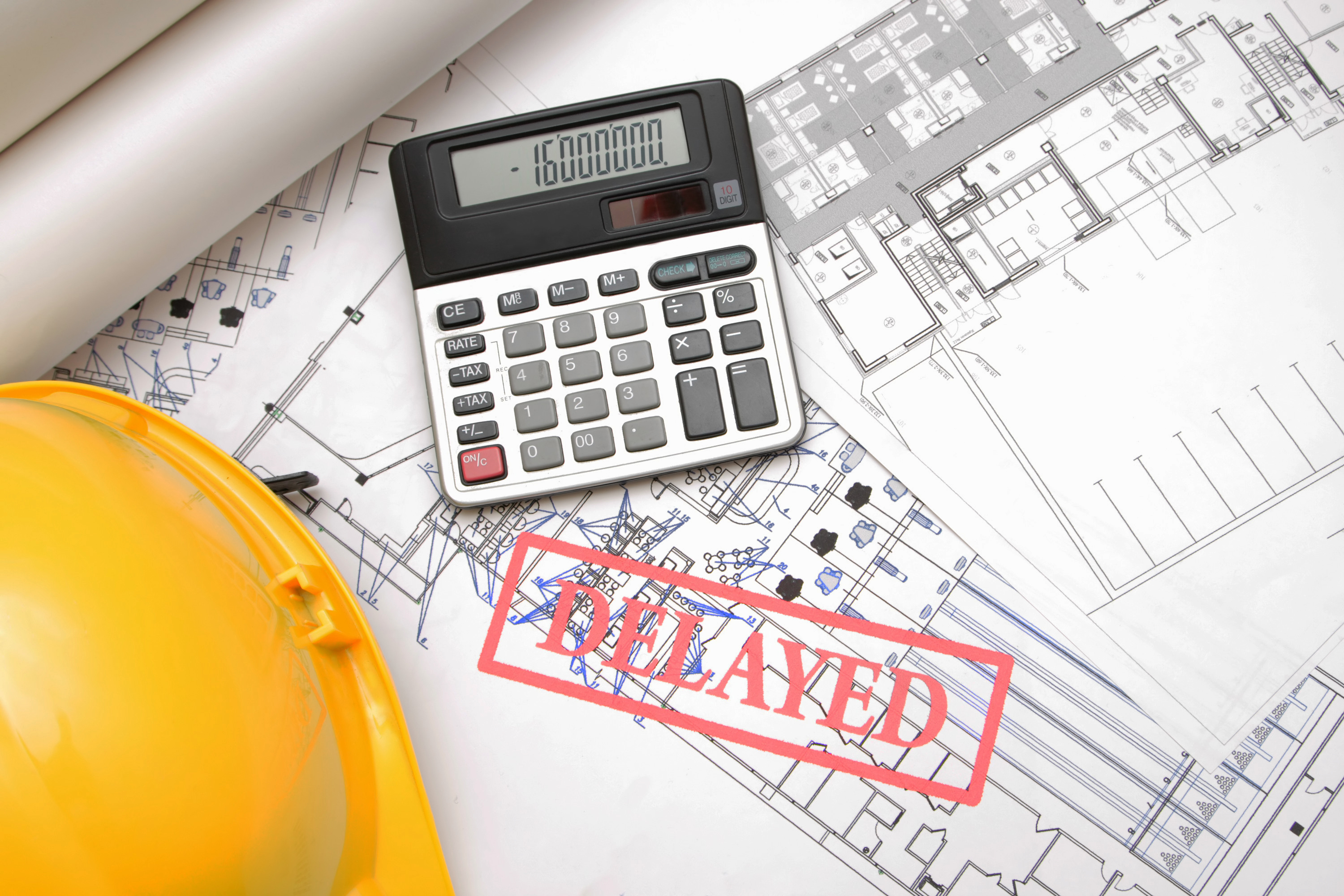
2. Inadequate Communication
Communication is key in construction projects where numerous stakeholders are involved. A lack of clear communication can result in misunderstandings, incorrect implementations, and ultimately, rework. Regular meetings, status updates, and effective communication channels can mitigate this issue. Utilizing project management software can also streamline communication, ensuring that everyone is on the same page.
3. Inaccurate Documentation
Accurate and up-to-date documentation is crucial for a smooth construction process. Incomplete or outdated documents can lead to errors in execution, requiring rework to correct. Ensure that all blueprints, plans, and permits are accurate and updated regularly. Implementing a robust document management system can help keep all documents organized and accessible.
4. Design Changes
Design changes are inevitable in construction, but they can be a significant cause of rework. To minimize this, establish a clear change management process. This should include evaluating the impact of changes, obtaining necessary approvals, and updating all relevant documents and plans accordingly.
5. Human Error
Human error is one of the most common causes of rework in construction. Mistakes can happen at any stage, from planning to execution. Training and continuous education for all team members can help reduce human errors. Implementing checklists and quality control measures can catch mistakes before they escalate into rework.
6. Using Inferior Materials
Using poor materials can compromise the quality of work, necessitating rework to replace or repair the structure. Always source materials from reputable suppliers. Using poor materials can compromise the quality of work, necessitating rework to replace or repair the structure. It's crucial to have access to a variety of high-quality materials to match the specific needs of each project. Bulk Exchange offers an extensive selection of bulk materials from top-tier suppliers, giving you the variety and choice you need to select the right materials for your project. Additionally, our platform features detailed ratings and reviews, allowing you to make informed decisions based on the experiences of other professionals. This ensures you’re not only getting the best materials but also the most reliable suppliers, minimizing the risk of rework.
7. Failure to Follow Standards
Construction projects must adhere to various standards and regulations. Failure to comply with these can result in rework to meet the required standards. Regular team training and audits can help maintain compliance.
8. Environmental Factors
Unpredictable weather conditions and other environmental factors can affect construction projects, causing delays and rework. While you can't control the weather, you can plan for it. Incorporate weather contingencies into your project plan and schedule tasks accordingly to minimize disruption.
9. Subcontractor Issues
Relying on subcontractors can introduce additional risks, including varying quality of work and adherence to schedules. Subcontractor issues can lead to rework if their work doesn't meet the project's standards. Vet subcontractors thoroughly before hiring; here are tips on how to vet subcontractors.
10. Improper Tools and Equipment
Using the wrong tools and equipment can lead to poor workmanship, resulting in rework to correct the issues. Make sure that all team members have access to the proper tools and equipment for their tasks. Regular maintenance and calibration of equipment can also help maintain quality.
11. Poor Site Management
Effective site management is crucial for a smooth construction process. Poor site management can result in disorganization, safety issues, and rework. Implementing a strong site management plan can help maintain order and efficiency as well as regular site inspections and safety checks can also help prevent issues that lead to rework.
Ways to Avoid Rework in Construction
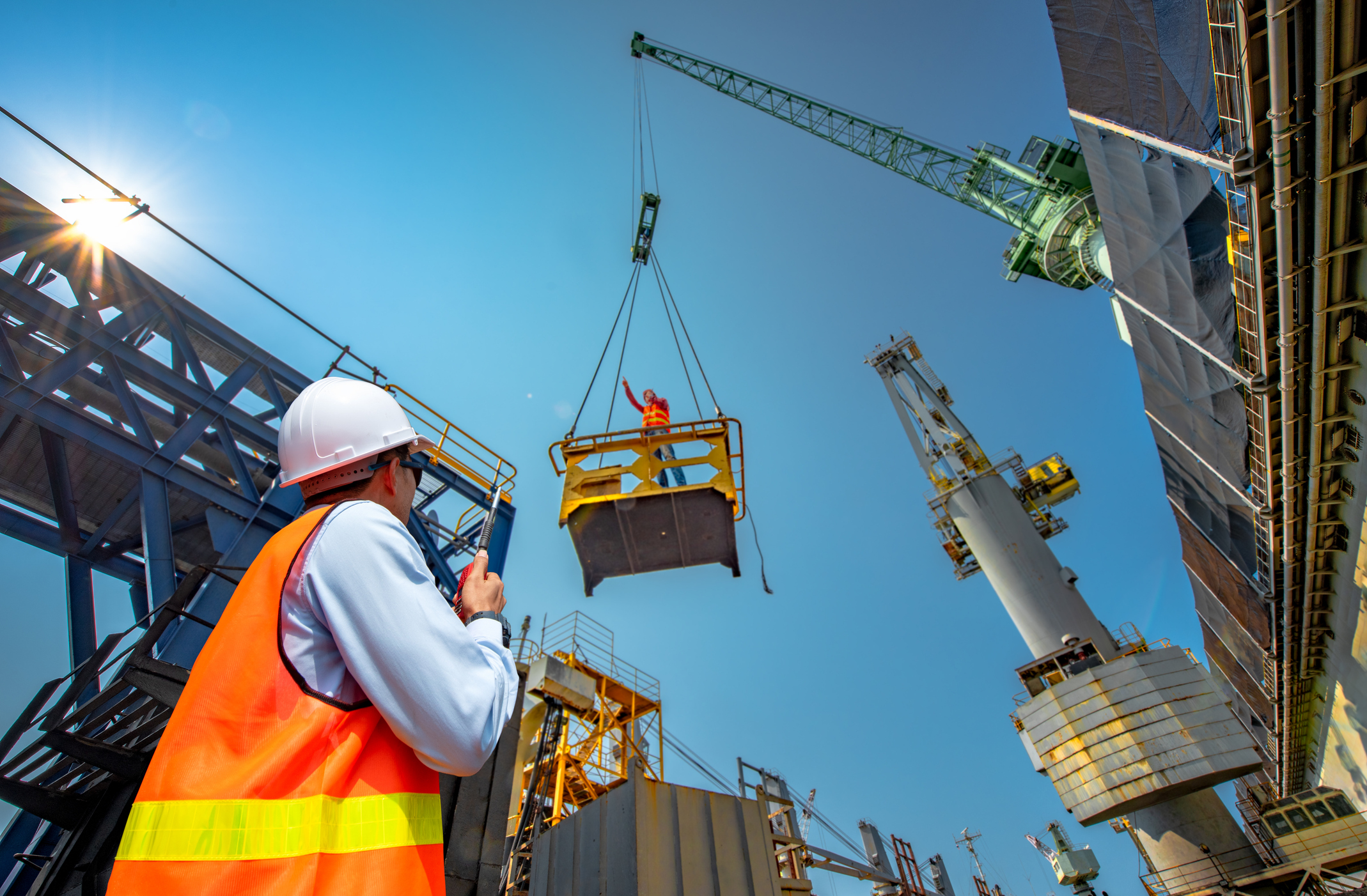
1. Have Clear Communication and Collaboration
Schedule regular meetings to ensure everyone is on the same page. Use these meetings to review progress, discuss potential issues, and clarify any concerns. Be sure to maintain detailed records of all project-related communications. This helps in mitigating misunderstandings and provides a reference point. Use any software that offers real-time communication and documentation sharing among project stakeholders.
2. Offer Training Programs
Regularly update your team’s skills through training programs. Focus on both technical skills and soft skills like communication. Ensure that all team members have up-to-date safety training and understand the significance of following protocols because safety lapses can lead to rework.
3. Enhance Quality Control
Regular inspections and audits help identify potential issues before they become major problems and ensures that all work adheres to industry standards and codes. Consider hiring external experts for unbiased reviews of your processes and work quality.
4. Leveraging Technology
Building Information Modeling (BIM) technology allows for comprehensive planning and visualization to manage schedules, track progress, and keep all team members informed, reducing the likelihood of errors. Construction management software apps allow for real-time updates and instant communication, making it easier to address issues as they arise.
5. Project Planning
Create detailed blueprints and project plans because the more thorough the plan, the fewer the chances for errors. Identifying potential risks at the outset and developing contingency plans is a proactive approach that can save time and money later on. Breaking a project into milestones and reviewing progress at each stage can also make it easier to catch and correct errors early.
6. Stakeholder Engagement
Regularly updating clients on project progress and involving them in key decisions ensures that the final product meets their expectations.
Rework in construction is a costly and time-consuming issue, but it can be mitigated with the right process in place. By understanding the common causes and implementing preventive measures, this will help your projects run smoothly and efficiently. Streamline Your Next Project—Get Started with Bulk Exchange for Free!