How to Know for Sure You’re Selecting the Best Local Supplier or Disposal Option
Choosing the right local supplier or disposal service will set your business up for success.
Read Article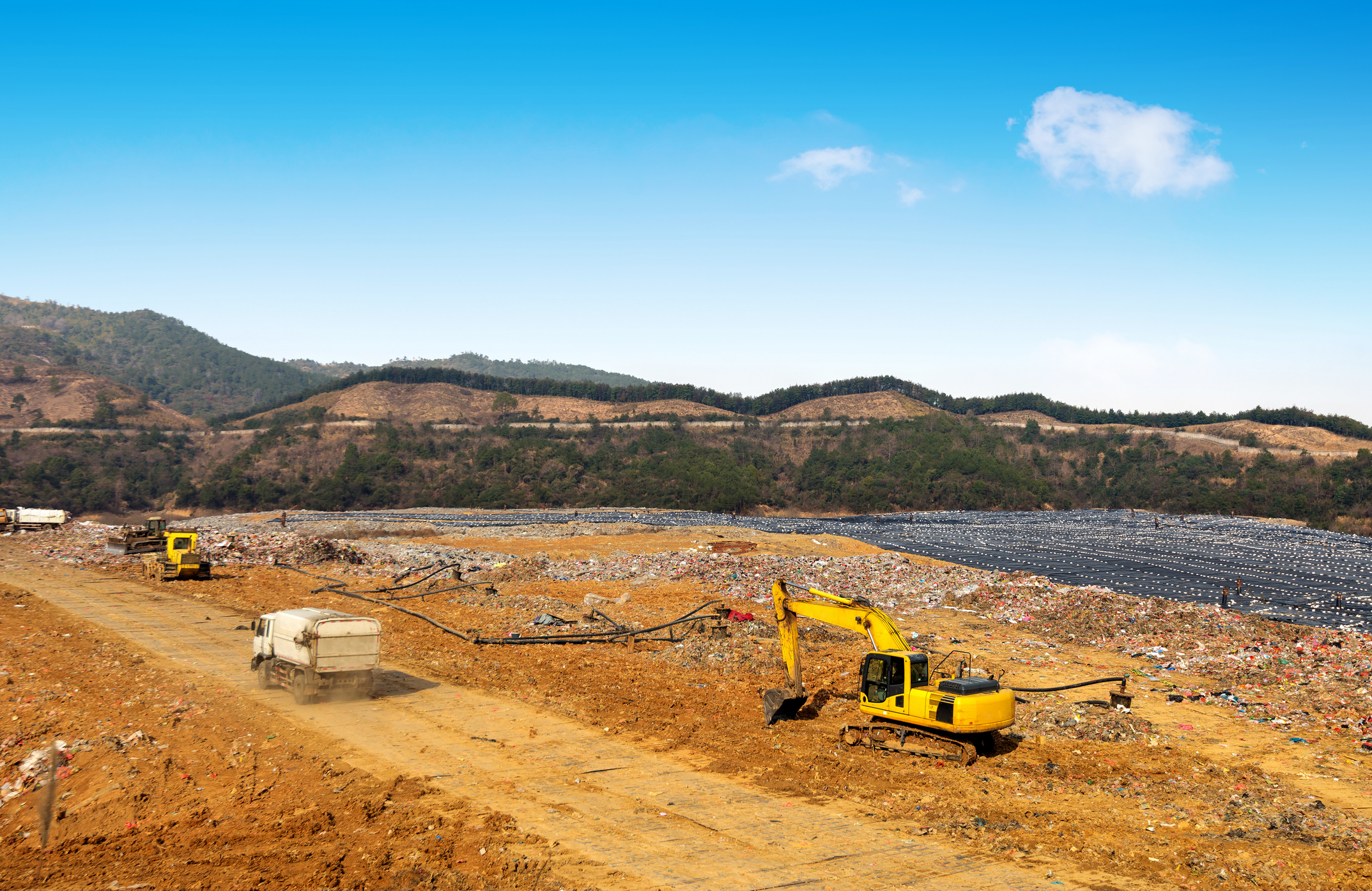
Choosing the right local supplier or disposal service will set your business up for success.
Read ArticleAsphalt is a composite material made up of aggregates, binder, and filler. The binder serves as a glue to hold the aggregate particles together, creating a solid, durable surface.
In construction, few materials are as pivotal as asphalt. Known for its versatility, durability, and cost-effectiveness, asphalt plays a crucial role in building the infrastructure that connects our communities and powers our economies. But what exactly is asphalt used for in construction? Learn the many ways in which asphalt is utilized.
Asphalt is a composite material made up of aggregates, binder, and filler. The binder serves as a glue to hold the aggregate particles together, creating a solid, durable surface. Asphalt is known for its ability to withstand heavy loads and harsh weather conditions, making it an ideal choice for various construction projects from schools to the Indianapolis Motor Speedway.
There are several types of asphalt, each suited for different projects. Here are four of the main types of asphalt:
The benefits of using asphalt are numerous. It's cost-effective, easy to install, durable, and requires minimal maintenance. Asphalt is also recyclable, making it a sustainable choice for construction projects.
These parking lots require a durable, long-lasting surface to withstand constant use. Asphalt provides just that, offering a smooth, attractive finish that can endure heavy traffic and harsh weather conditions. Its quick installation time also means businesses can resume operations faster.
For residential driveways, asphalt offers a clean, aesthetically pleasing option. Its durability ensures it will last for years with minimal upkeep, and its flexibility allows it to adapt to ground movements, preventing cracks and potholes.
Industrial parking areas often see a lot of heavy machinery and vehicles. Asphalt can handle the weight and stress of industrial parking areas, providing a reliable and low-maintenance solution.
Airport runways need materials that can withstand extreme stress and varying weather conditions. Asphalt's flexibility allows it to accommodate the movements of large aircraft without cracking, ensuring a safe and smooth surface for taxiing planes.
Airport aprons, where planes are parked, loaded, and unloaded, require a strong surface. Asphalt's durability and low maintenance make it the best choice for airport aprons.
Pedestrian walkways constructed from asphalt provide a smooth, safe surface for walking. The material's flexibility allows it to adapt to ground movements, preventing cracks, ensuring durability
Bicycle paths benefit from asphalt's smooth surface by providing a comfortable ride for cyclists. The material's durability ensures the path can withstand constant use, while its low maintenance needs make it a cost-effective option for municipalities.
Recreational trails made from asphalt offer a reliable surface for walking, running, and biking. The material's ability to withstand various weather conditions and heavy use ensures that trails need minimal upkeep.
Industrial storage areas require a robust, durable surface to withstand heavy machinery and constant use. Asphalt provides just that, offering a low-maintenance, long-lasting solution for industrial environments.
Loading docks see constant use and heavy loads, requiring a strong, reliable surface. Asphalt's durability and flexibility make it an ideal choice for loading docks, ensuring a smooth, safe area for loading and unloading goods.
Manufacturing plants benefit from asphalt's properties, providing a durable, low-maintenance surface for heavy machinery and constant use. The material's flexibility allows it to adapt to ground movements, preventing cracks and damage.
From highways to airports to pedestrian walkways, asphalt plays a vital role in modern construction. Its versatility, durability, and sustainability make it an indispensable material for construction professionals and civil engineers. Understanding the various applications and benefits of asphalt can help you make informed decisions for your projects, ensuring long-lasting, high-quality results.
Here are effective strategies for minimizing environmental impact in large civil construction projects. Find out how Bulk Exchange can help with your project.
With rapid urbanization and infrastructure development, the environmental impact of large civil construction projects has become a pressing issue. It’s more important than ever for industry professionals to implement sustainable practices. Learn ways to minimize your construction projects’ ecological footprint by using sustainable building materials.
Construction is a major driver of economic development, but it also poses significant environmental challenges. This sector is responsible for a substantial portion of global carbon emissions and waste production. Understanding these impacts is the first step in mitigating them effectively.
Two primary areas of concern are resource consumption and waste generation. Large construction projects often require vast amounts of materials like concrete, steel, and water, leading to resource depletion. Additionally, waste generated from construction sites contributes to landfill burdens and pollution.
The impact isn't limited to resource use and waste. Construction activities can disrupt local ecosystems, affect biodiversity, and cause air and water pollution. To address these issues, stakeholders must adopt a holistic approach, considering both the immediate and long-term environmental effects.
Navigating the complex landscape of environmental regulations is important to understand sustainable construction. International and local guidelines exist to ensure that construction practices minimize harm to the environment. Regulatory frameworks like the National Environmental Policy Act (NEPA) were enacted to ensure that federal agencies thoroughly consider the environmental impacts of their proposed actions before making decisions, requiring them to prioritize environmental factors alongside other considerations when planning projects. This was in response to growing public concern about the deteriorating quality of the environment and inadequate consideration of environmental impacts in major federal projects. Impact Statements (EISs) and Environmental Assessments (EAs) to assess the potential impacts of different courses of action.
In addition to legal requirements, numerous voluntary standards and certifications can guide construction projects. Certifications like Leadership in Energy and Environmental Design (LEED) encourage the adoption of sustainable practices by assessing various criteria such as energy efficiency, water use, and waste management.
Pre-Project EIA: Conduct comprehensive assessments to identify potential impacts on soil, water, air, and biodiversity. This analysis should inform the project’s design and decision-making.
One of the most exciting aspects of sustainable construction is the innovation in materials and technologies. Green materials are emerging as viable alternatives to traditional building materials, offering reduced environmental footprints and enhanced performance. For instance, green concrete is a sustainable alternative to traditional concrete that uses recycled materials and requires less energy to produce. Likewise, Cross-Laminated Timber (CLT) offers a renewable alternative to concrete and steel, providing structural integrity while storing carbon.
Technological advancements are also playing a crucial role in minimizing construction's environmental impact. Drones and sensors enable real-time monitoring of construction sites, improving efficiency and reducing waste. Meanwhile, Building Information Modeling (BIM) allows for precise planning and resource management, minimizing environmental impact.
Energy consumption during construction and operation phases is a significant contributor to environmental impact. To help reduce your carbon footprint, construction companies can adopt strategies like prefabrication which reduces energy use by assembling components off-site in controlled environments. This not only minimizes energy consumption, but also decreases waste and transportation emissions.
Incorporating renewable energy sources like solar panels and wind turbines into construction sites can further help with energy efficiency. These technologies provide clean energy to power construction activities, reducing reliance on fossil fuels.
Construction projects can strain local water supplies if not managed carefully, so efficient water management strategies are essential for sustainable construction. Some water management strategies for construction include: rainwater harvesting, greywater recycling, using water-saving fixtures like low-flow taps and dual-flush toilets, implementing smart irrigation systems, and proper soil management.
Waste management is a key aspect of sustainable construction. By minimizing waste generation and promoting recycling, construction projects can significantly reduce their environmental impact. On-site waste separation is a good strategy for managing waste efficiently. By sorting materials like wood, metal, and concrete, construction companies can divert waste from landfills and send it to recycling facilities. Construction waste can also be repurposed into new building materials, reducing the need for more resources.
The field of sustainable construction is constantly evolving, driven by technological advancements and changing consumer expectations. Staying informed about future trends will help you remain competitive and environmentally responsible.
Some of other emerging trends include:
It’s important to continuously monitor and audit the environmental impact your construction project has. Use air quality monitors, noise sensors, and water quality testers to track the environmental impact in real time. Implement systems Environmental Management Systems (EMS) like ISO 14001 to streamline environmental management processes and ensure compliance. Make sustainable building choices in an effort to help keep the environment clean.
Are you starting a construction project and need to find the right material? We can help you source the material you’ll need for your project and have also added a carbon calculator feature so you can make the right financial and environmental choice for your project. Get started with Bulk Exchange for free today!
Are you a fleet manager looking to improve efficiency and reduce costs? Here are the metrics every fleet manager should track.
Fleet management is more than just keeping track of vehicles and drivers. For fleet managers, knowing which metrics to monitor can make the difference between smooth operations and costly disruptions. In this blog post, we’ll explore the key metrics every fleet manager should be tracking to gain insights into operations, and ensure efficiency, safety, and profitability.
Regular maintenance is essential for keeping your fleet in top condition, extending the life of your assets, reducing the expenses associated with major repairs, and increasing your operational efficiency. Whether you handle maintenance internally or use a third-party service provider, keeping an eye on the duration vehicles spend in the workshop ensures that repairs are executed promptly.
Avoiding interruptions should always be a top priority for fleet managers, so when vehicles are left in the garage for several days, it's natural to worry that this is affecting schedule and potential revenue loss. According to CEREBRUMX, it’s “estimated that fleets lose an average of $448 to $760 a day, per vehicle, or $79.33 per hour due to vehicle downtime.”
Considering the expenses associated with repairs, it's crucial to recognize how unforeseen equipment failures can affect your financial plan. While unexpected repairs will arise, evaluate them in comparison to your scheduled maintenance and see if they can be done together.
Driver Vehicle Inspection Reports (DVIR) play a crucial role in maintaining compliance and notifying supervisors about any problems with vehicles. However, they also offer a valuable tool for assessing the condition of your assets. By utilizing DVIR information and examining it for patterns among different users or vehicles, you can gain significant insights into the well-being of your assets.. Monitoring the rate at which inspections are completed can assist in verifying that drivers are conducting inspections diligently and that you are gathering essential data points at each asset.
Simply finishing inspections isn't sufficient; recognizing how your fleet's operations connect to the pass or fail rates of your inspections can quickly highlight areas needing enhancement. If vehicles keep passing inspections but eventually need repairs, it might suggest a lack of comprehensive inspections. Conversely, a vehicle that consistently fails inspections might signal that it has reached the end of its service life in your fleet.
Regarding planned and unplanned maintenance, the amount of time your vehicles spend not in use is mainly due to maintenance activities. If a vehicle is being kept in the garage longer than it's on the road, it might suggest that it's time to consider replacing it because this could be affecting your ROI.
Your mileage tracker will help you know when to schedule preventive maintenance and decide when to replace vehicles. Since many preventive maintenance activities are scheduled based on mileage and hours, getting frequent updates on mileage helps you maintain your fleet's performance. Additionally, you can utilize mileage data to better manage your drivers and reduce expenses on fuel.
Fuel is one of the largest ongoing costs associated with running a fleet, making it essential to meticulously monitor both usage and expenditure. Implementing a system to continuously track and compute the costs of fuel and its usage can enhance your approach to managing fuel. Fuel consumption can be tracked by GPS, telematics software, fuel flow meter, and fuel level sensors.
Fleet utilization is a benchmark to determine the percentage of how much a fleet vehicle is being used in comparison to its maximum potential. Once the percentage is determined, fleet managers can examine existing operations to pinpoint areas of inefficiency and implement any improvements.
Tracking your fleet's actual Total Cost of Ownership (TCO) might be the most crucial and detailed measure you need to monitor. This is a difficult area to keep an eye on and control, yet being aware of your fleet's TCO empowers you to make informed choices based on data. Analyzing your fleet's costs provides insight into your investment's ROI. It also aids in planning for regular maintenance, deciding when to replace vehicles, and choosing between buying or leasing new ones.
Cost Per Mile (CPM) is a measure that determines the expenses related to the operation of a single vehicle or an entire fleet over a certain distance, usually measured in miles. Fleet supervisors use CPM as a key metric to track and control the efficiency and cost-effectiveness of their vehicle fleets. An increase in CPM suggests that a vehicle or fleet may not be as efficient as it once was or it may not be delivering the same value.
Data on CPM helps with budget planning, predicting financial outcomes, and facilitating better management of resources. By grasping CPM, fleet supervisors can identify specific areas of vehicle performance that require enhancement and make informed choices regarding the fleet's composition based on data.
If you're in charge of maintenance yourself, it's important to use the right equipment⎯even if it costs more, to lessen the time vehicles spend out of service. Monitoring your inventory of parts is key to preventing shortages and cutting down on the costs associated with excess stock. Consistently checking the history of orders for parts and monitoring the value of your inventory helps make informed decisions about future expenditures.
Telematics data gives important insights into fleet visibility and the condition of assets. This data helps gather driver behavior, vehicle location and activity, and engine performance, allowing for the proactive oversight of driver actions and the detection of anything that could endanger both the driver and the vehicle.
While those in charge of fleets concentrate a lot on their vehicles, it's equally crucial to monitor and oversee your drivers. Allocating vehicles to drivers enables you to easily access information about the length and distance of their trips. By connecting other systems such as telematics and fuel cards to a fleet management application, you can gain a detailed understanding of a driver's performance by observing their location, habits, and expenditures.
The future of fleet management lies in data-driven decision-making. By staying ahead of trends and continuously monitoring key metrics, you can ensure that your fleet operations remain efficient, safe, and profitable.
As sustainability becomes more important, learn why ESG matters for construction companies.
The construction industry isn’t just about buildings and infrastructure, but it’s becoming increasingly important to consider the broader impact of these projects on the environment, society, and governance (ESG). What is ESG in construction, and why is it important? Learn why construction companies should adopt ESG principles for sustained success and business growth.
ESG stands for Environmental, Social, and Governance. These three pillars represent the key areas of focus for sustainable and responsible business practices. In the context of construction, ESG encompasses a wide range of considerations such as:
Adopting ESG principles in construction is not just a trend but a necessity for the industry's future. The construction industry has been criticized for its environmental impact. Integrating ESG principles can address these concerns by promoting sustainable building practices and transparent governance. This not only enhances a company’s reputation, but also makes it more attractive to investors who are increasingly prioritizing ESG criteria. According to Morgan Stanley, “more than half of individual investors say they plan to increase their allocations to sustainable investments in the next year, while more than 70% believe strong ESG practices can lead to higher returns.”
Governments and regulatory bodies worldwide are increasingly mandating ESG compliance. The European Union's Sustainable Finance Disclosure Regulation (SFDR) requires companies to disclose their ESG performance. In March, the U.S. Securities and Exchange Commission (SEC) adopted a new rule that requires publicly traded companies to disclose climate-related information in their annual reports and financial statements.
One of the most critical aspects of ESG in construction is sustainable design. This involves using eco-friendly materials, optimizing energy consumption, and minimizing waste. Green building certifications like Leadership in Energy and Environmental Design (LEED) and Building Research Establishment Environmental Assessment Method (BREEAM) are great benchmarks for sustainability.
Energy efficiency is another crucial component of environmental sustainability. Implementing energy-efficient systems and technologies can significantly reduce the carbon footprint of a construction project. For example, using solar panels, energy-efficient HVAC systems, and smart lighting can contribute to a greener project.
Effective waste management helps minimize the environmental impact of construction activities. This includes recycling and reusing materials, reducing construction waste, and implementing waste-to-energy solutions. Companies like Waste Management Inc. offer comprehensive waste management services tailored to the construction industry.
Integrating ESG principles into construction projects starts at the planning and design stage. This involves conducting environmental impact assessments, engaging with stakeholders, and setting clear ESG objectives. Collaboration with architects, engineers, and sustainability experts is important for the project's overall success.
Choosing the right suppliers and contractors is important to meet ESG goals. Companies should evaluate potential partners based on their ESG performance, ethical practices, and commitment to sustainability. This due diligence can help ensure that all project participants align with ESG objectives.
Continuous monitoring and evaluation involves setting Key Performance Indicators (KPIs), conducting regular assessments, and making necessary adjustments.
Technological advancements will play a crucial role in the future of ESG in construction. Innovations like Building Information Modeling (BIM) and AI can enhance sustainability, improve efficiency, and support better decision-making. Companies that invest in these technologies will be better positioned to meet ESG goals.
The regulatory landscape for ESG is continuously evolving. Companies must stay updated on new laws and regulations and adapt their practices accordingly. Proactive compliance can help mitigate risks and ensure long-term success.
Stakeholders, including investors, customers, and employees are increasingly prioritizing ESG. Companies that demonstrate a strong commitment to ESG will be better positioned to attract investment, win contracts, and build lasting relationships.
By prioritizing environmental sustainability, companies can achieve better project outcomes, company reputation, and contribute to a more sustainable world. Make ESG principles in your construction projects for continued growth and success for your business.
Reducing waste in construction is crucial for several reasons including, environmental sustainability, cost efficiency, and resource conservation.
Reducing waste in construction is crucial for several reasons including, environmental sustainability, cost efficiency, and resource conservation. With the goal of creating a more sustainable environment, it’s important to understand why reducing material waste in construction projects is essential. Find out how to reduce material waste in this blog.
Construction waste can include a wide range of materials such as concrete, bricks, wood, metal, insulation, and glass. It often results from excess materials ordered, off-cuts, or materials damaged during construction activities.
Waste management in construction is a challenge that the industry has been grappling with for years. Without proper planning and conscious effort, construction sites can produce vast amounts of waste that contribute to landfill overflow and environmental pollution.
Proper waste management can significantly reduce the amount of waste that ends up in landfills, reducing the industry's carbon footprint and conserving natural resources by recycling and reusing materials.
Reducing waste can lead to substantial cost savings. By estimating the amount of materials you’ll need and reusing and recycling where possible, construction companies can reduce purchase costs and disposal fees.
Many regions have strict regulations regarding waste disposal and recycling. Learn more about the federal environmental requirements for construction here.
Demonstrating a commitment to reducing waste can enhance your brand and attract more eco-conscious customers.
A waste management plan for a construction project is a blueprint for how materials will be managed on-site. It should detail the types of waste expected, how it will be handled, and the disposal or recycling methods.
Ordering the correct amount of materials and handling them properly can greatly reduce waste. Use just-in-time delivery systems to prevent material spoilage on-site and plan for material storage to protect them from damage.
Design plays a critical role in waste management. Designing buildings and infrastructures with precise measurements can prevent the over-ordering of materials.
Whenever possible, choose deconstruction over demolition. Deconstruction allows for the careful dismantling of buildings to salvage materials for reuse or recycling, rather than demolishing them and sending the materials to a landfill.
To make a construction waste management plan effective, here are some ideas on how to implement it.
Train your workforce on the importance of waste management and how they can contribute to reducing waste. Awareness is key to ensuring that everyone follows the waste management plan.
On-site segregation of waste materials is essential. Provide different bins for various types of waste and ensure they are clearly labeled. This makes recycling and disposal more manageable and more efficient.
Regularly monitor waste levels and report on waste management outcomes. This will help identify areas for improvement and ensure the waste management plan is being followed.
Lean construction encourages continuous improvement through regular reviews and updates of waste management practices. Learn from each project and refine your strategies accordingly.
Despite the clear benefits, there are challenges in reducing waste in construction. These include:
A lack of knowledge or expertise in waste management can hinder the implementation of effective strategies.
Sometimes the upfront costs of waste management practices such as purchasing recycling equipment can be a deterrent.
The logistics of dividing, storing, and transporting waste for recycling can be complex, especially on constrained sites.
With continued innovation and commitment, the construction industry can minimize its environmental impact, save costs, and contribute to a more sustainable future.
Switching your business to a paperless system means replacing physical documents with cloud-based software solutions for everything from blueprints to contracts.
In the world of construction where deadlines are tight and margins can be thin, efficiency is key to running your business. Yet, many construction companies still rely on paperwork to manage projects. Transitioning to a digital project management solution can streamline operations and reduce overhead. Learn more about the benefits of a paperless system so you can move towards a more efficient construction business.
Switching your business to a paperless system means replacing physical documents with cloud-based software solutions for everything from blueprints to contracts. By adopting these technologies, construction businesses can save time, reduce costs, and streamline processes.
Paper-based systems are often cumbersome and time-consuming. Digital tools allow for quicker access to information, seamless communication, and real-time updates. This means less time spent searching for documents and more time focusing on the project.
Printing, storing, and managing paper documents can be expensive. By going paperless, construction companies can significantly cut down on these costs.
Keeping up with compliance and reporting requirements can be complex. Digital tools can streamline this process by automating compliance checks and generating reports. This ensures that your company meets all regulatory requirements without extra effort.
Eco-conscious businesses recognize the importance of reducing their carbon footprint. Going paperless is a significant step towards sustainability, as it minimizes the use of paper and reduces waste. This not only benefits the environment but also enhances the company's reputation as a green business.
Cloud-based solutions enable team members to collaborate from different locations. Whether working on-site or remotely, everyone can access the same information and contribute to the project in real-time. This leads to better teamwork and more efficient project management.
By switching to cloud-based software for construction projects, team members can access important documents on their phones or tablets which means that even when they're on a site, they can review plans, update progress, and communicate with the team.
The first step in going paperless is selecting the right software. Look for solutions that offer project management, reporting, system integration, storage, mobile compatibility, and collaboration features.
Transitioning to a paperless system requires training, so it’s important to ensure your team has the right training so they feel confident using the software.
Finding specific documents in a mound of paperwork can be challenging. Cloud storage solutions offer easy retrieval through search functions, tags, and organized folders⎯this will save a lot of time.
Security is a concern for construction companies. Cloud solutions offer secure storage with encryption and access controls. This ensures that sensitive information is protected from unauthorized access.
A report on LinkedIn states that “an estimated $273 billion worth of construction errors made each year in the U.S. alone, which leads many construction firms to bake rework into the cost of construction, creating a contingency budget.” This is where cloud-based software comes in because it can automate workflows, such as approvals and notifications, to reduce delays caused by manual processes.
Going paperless is a significant step toward modernizing your company and staying competitive in the construction industry. There will be an initial investment in the technology and training of your team, but the long-term advantages make it advantageous to adopt a paperless company.
The construction industry is experiencing rapid technological advancements, reshaping how projects are designed, managed, and executed.
The construction industry is experiencing rapid technological advancements, reshaping how projects are designed, managed, and executed. Construction professionals must understand the emerging technologies that will enhance efficiency and sustainability. Here are some key construction technology trends and innovations shaping its future.
Sustainability continues to be a driving force in the construction industry. In 2024, expect to see an increased focus on eco-friendly materials and methods. Companies are prioritizing the use of recycled materials, energy-efficient building systems, and designs that minimize environmental impact. Our marketplace supports this trend by offering a wide range of sustainable bulk materials, ensuring that your projects meet regulatory requirements and contribute to a greener future.
Building Information Modeling (BIM) has been a game-changer for the construction industry, and its capabilities are expanding. In 2024, BIM will become even more integral to project planning and execution. Enhanced 4D and 5D BIM tools will allow for better visualization of project timelines and cost management, leading to more accurate forecasting and resource allocation. Our platform integrates seamlessly with BIM systems, providing real-time data on material availability and pricing.
Artificial Intelligence (AI) and machine learning (ML) are set to revolutionize construction management. These technologies can analyze vast amounts of data to predict project outcomes, optimize workflows, and identify potential risks before they become issues. For instance, predictive analytics can help plan material orders, reduce waste, and ensure timely delivery.
AI and ML will also play a crucial role in enhancing safety on construction sites. Advanced analytics can identify patterns and trends in safety data, allowing companies to implement targeted interventions to reduce accidents. Additionally, AI-powered surveillance systems can monitor construction sites in real time, detecting hazardous conditions and alerting workers immediately.
Our marketplace leverages AI to provide intelligent recommendations and insights, making your procurement process smarter and more efficient.
Robotics and automation are transforming construction sites into hubs of efficiency and precision. Autonomous construction equipment such as drones, bulldozers, and excavators will become more prevalent. These machines can perform tasks like site surveying, earthmoving, and material handling with minimal human intervention, reducing labor costs and increasing productivity.
The future of construction technology brings numerous advancements to the industry that will transform how projects are designed, managed, and executed. From BIM enhancements and robotics to sustainable practices and AI-powered solutions, construction professionals have many tools to improve efficiency, safety, and sustainability. As these technologies continue to evolve, staying informed and adapting to the latest trends will be crucial for success in the competitive construction industry. Embrace the future of construction technology, and position yourself at the forefront of innovation. Learn more about how we can help you!
Learn about the rise of private equity firms in the heavy civil construction industry.
The heavy civil construction industry, known for building critical infrastructure like roads, bridges, and utilities, is undergoing a transformation. Private Equity (PE) firms and corporate consolidation are reshaping the industry’s landscape, influencing everything from business operations to workforce dynamics. While these trends bring opportunities for growth and efficiency, they also introduce challenges that demand attention.
Private equity firms have increasingly recognized the heavy civil construction sector as a lucrative investment opportunity. Infrastructure spending remains a government priority, with significant funding initiatives such as the U.S. Infrastructure Investment and Jobs Act (IIJA) creating a steady demand for construction services.
1. Predictable Revenue Streams: Government contracts for infrastructure projects often provide long-term, stable cash flows that attract investors.
2. Fragmented Market: The heavy civil construction industry is highly fragmented, with many small to mid-sized firms. PE firms see opportunities to acquire and consolidate these businesses to create economies of scale.
3. Growth Potential: Advancements in technology, sustainability, and urbanization offer avenues for innovation and expansion, making the sector a promising area for investment.
Consolidation—the merging of smaller firms into larger entities—has accelerated under private equity influence. While this trend can drive efficiency and create larger, more competitive firms, it also has ripple effects on the industry.
1. Increased Efficiency: Consolidated firms often benefit from centralized operations, shared resources, and improved purchasing power, lowering costs.
2. Access to Capital: Larger entities backed by private equity have greater financial resources to invest in technology, equipment, and talent.
3. Standardization and Innovation: Mergers can drive the adoption of best practices and new technologies, enhancing project quality and delivery.
1. Reduced Competition: As smaller players are absorbed, competition in the market diminishes, potentially leading to higher project costs for clients. New marketplaces like Bulk Exchange help counteract this disadvantage by providing easier access to list prices and supplier locations.
2. Cultural Shifts: Mergers often bring cultural clashes and changes in management styles, which can disrupt operations and workforce morale.
3. Pressure for Profitability: Private equity investors expect high returns, which can lead to cost-cutting measures, including workforce reductions or prioritization of short-term gains over long-term stability.
The influence of private equity and consolidation is felt acutely by the workers who build the nation’s infrastructure.
• Larger firms often prioritize automation and efficiency, potentially reducing demand for certain skilled trades.
• Smaller, family-owned businesses—which have traditionally dominated the industry—are disappearing, taking with them a focus on local hiring and community relationships.
Consolidation can create opportunities for standardized training and career growth within larger organizations. However, cost pressures may limit investment in workforce development.
Frequent ownership changes and cost-cutting measures associated with private equity investments can create uncertainty for employees, leading to higher turnover and reduced morale.
Private equity and consolidation are also influencing broader industry strategies:
Larger, PE-backed firms are more likely to invest in cutting-edge technology such as centralized marketplaces and data hubs like Bulk Exchange, Building Information Modeling (BIM), AI-driven project management, and drone-based surveying, setting new industry standards.
Private equity firms are pushing investments in sustainable infrastructure, such as renewable energy projects and eco-friendly construction practices, to align with environmental goals and market demands.
Consolidated firms are better positioned to expand geographically, enabling them to bid on larger, more complex projects across multiple states or regions.
The growing influence of private equity and consolidation in heavy civil construction is reshaping the industry in profound ways. To navigate this evolving landscape:
• Firms must adapt: To stay competitive, smaller players should explore strategic partnerships, niche specializations, or investments in technology.
• Workforce development is key: The industry must prioritize training programs to ensure workers are prepared for the changing demands of larger, more tech-driven organizations.
• Policymakers should monitor consolidation: Ensuring a competitive market and protecting workers’ interests will be critical as the industry evolves.
Private equity and consolidation are undeniably shaping the future of heavy civil construction. While these trends bring opportunities for innovation, efficiency, and growth, they also come with challenges that must be addressed. The industry can build infrastructure and a stronger and more resilient future by embracing change while safeguarding competition, workforce stability, and community relationships.
Heavy civil construction stands at a crossroads—how the industry adapts now will determine its trajectory for decades to come.
About the Author
Rachael Mahoney is the Chief Strategy Officer at Bulk Exchange. With extensive experience in the construction and technology sectors, she is passionate about driving innovation and fostering sustainable growth in the heavy civil construction industry. Follow Rachael for more insights on LinkedIn .
Learn why expanding your talent pool in heavy civil construction is crucial for success and growth in this post.
The heavy civil construction industry, which forms the backbone of infrastructure development, faces a pressing challenge: a growing labor shortage. The demand for skilled workers continues to outpace supply, threatening timelines, budgets, and overall productivity. While efforts to address this gap often focus on traditional recruitment pipelines, the solution lies in reimagining who belongs in the industry. Building a bigger tent—one that actively welcomes women, LGBTQ individuals, and other historically underrepresented groups—is essential for the industry to thrive.
Currently, women represent less than 11% of the construction workforce, and LGBTQ professionals, along with other marginalized groups, face barriers such as stigma, lack of representation, and limited visibility in leadership roles. The industry can tap into a vast pool of talent and currently underutilized perspectives by opening doors to these populations. Inclusion isn’t just about numbers; it’s about enriching the industry with diverse ideas, innovative solutions, and resilient workers ready to build the infrastructure of tomorrow.
Several factors deter underrepresented groups from joining the construction industry:
1. Cultural Norms: Stereotypes about construction being a male-dominated, physically demanding field can dissuade women and LGBTQ individuals from considering careers in the sector.
2. Lack of Visibility: When job sites and leadership teams lack representation, prospective workers may not see a place for themselves in the industry.
3. Workplace Environment: Concerns about discrimination, harassment, or lack of support can create barriers to retention even after individuals enter the field.
4. Limited Outreach: Traditional recruitment efforts often overlook diverse talent pipelines, missing opportunities to engage with these groups.
Creating a more inclusive industry isn’t just the right thing to do—it’s a strategic imperative. Here’s why:
• Solving Labor Shortages: Broadening the recruitment pool to include underrepresented groups can help fill critical roles at every level, from skilled trades to management.
• Boosting Innovation: Diverse teams bring a wider range of perspectives, leading to more creative problem-solving and better decision-making.
• Reflecting Society: Infrastructure projects serve all people. A workforce that mirrors the communities it serves fosters trust and enhances project outcomes.
1. Education and Outreach:
Promote construction careers to diverse audiences early, starting in high schools, community colleges, and job fairs. We at Bulk Exchange recently hosted the first of a series of events, bringing together the Concrete Industry Management and Construction Management programs at Chico State as an example of progress through collaboration and outreach. Partnerships with organizations advocating for women, LGBTQ individuals, and minority groups can amplify these efforts.
2. Creating Inclusive Workplaces:
Foster an environment where everyone feels safe and valued. This includes enforcing zero-tolerance policies for harassment, providing diversity training, and offering mentorship programs.
3. Representation Matters:
Highlight diverse role models within the industry through marketing, speaking engagements, and leadership development programs—representation at the top signals that inclusion is a priority.
4. Flexible Policies:
Accommodate diverse needs, such as offering parental leave, flexible schedules, and accessible job sites. These policies make construction careers more attractive to a broader range of individuals.
The heavy civil construction industry is at a crossroads. Addressing labor shortages requires more than filling open roles—it demands a cultural shift toward greater inclusivity. By building a bigger tent, the industry can not only attract underrepresented groups but also foster innovation, resilience, and long-term success.
If the industry embraces this challenge, it will pave the way for a stronger workforce and a brighter future for everyone. Let’s build it together.
About the Author
Rachael Mahoney is the Chief Strategy Officer at Bulk Exchange. With extensive experience in the construction and technology sectors, she is passionate about driving innovation and fostering sustainable growth in the heavy civil construction industry. Follow Rachael on LinkedIn for more insights.
Discover why modernizing heavy civil construction is crucial for the industry's growth and success.
The heavy civil construction industry is a cornerstone of society and a symbol of resilience. From building roads and bridges to water systems and ports, this sector has long relied on human ingenuity and grit to create the infrastructure that powers daily life. But as the world becomes more complex, the industry faces new challenges: labor shortages, rising costs, tight timelines, and increasing demands for sustainability.
Modernizing heavy civil construction through technological solutions like Bulk Exchange, an online marketplace and industry-specific search tool, is no longer a luxury—it’s a necessity. However, this evolution must honor the industry’s deep-rooted tradition of interpersonal relationships, which remain the foundation of successful projects. The future of heavy civil construction lies at the intersection of innovation and connection.
With an aging workforce and a struggle to attract younger talent, the industry is in dire need of solutions that ease labor demands. Automation and technology can fill gaps by taking on repetitive or high-risk tasks, allowing human workers to focus on roles requiring creativity, leadership, and decision-making.
Technological advancements such as AI-driven project management, Building Information Modeling (BIM), and automated machinery can streamline operations. These tools help reduce errors, optimize resource allocation, and shorten project timelines—all of which are critical in an industry where time is money.
Modern technology enables sustainable construction practices, such as energy-efficient designs, waste reduction, and eco-friendly materials. Automation can also improve precision, reducing material waste and carbon footprints.
In a globalized economy, firms that fail to embrace innovation risk falling behind. Adopting modern tools and practices ensures companies remain competitive when bidding on projects, especially those requiring advanced capabilities.
Robotics and automated equipment are transforming construction sites. Autonomous excavators like those from Built Robotics, drones for site surveys, and robotic arms for repetitive tasks like bricklaying enhance safety and efficiency while addressing labor shortages.
Data-driven decision-making is a game changer. Bulk Exchange was founded largely to address the lack of connection between the supply and demand sides of the industry and to create a rich data collection opportunity that would return value to both. Richer data is needed to enable predictive analytics to identify risks before they become problems, while AI-powered scheduling tools optimize timelines and budgets.
BIM allows for collaborative digital design and planning. It ensures all stakeholders—from engineers to contractors—have access to a shared, real-time model of the project, improving communication and reducing costly misunderstandings.
Technologies like 3D printing, energy-efficient equipment, and material recycling solutions help the industry align with environmental standards while reducing costs.
While technology transforms how projects are built, relationships remain the cornerstone of success in heavy civil construction. Modern tools cannot replace the trust, collaboration, and problem-solving that come from human connection.
Clear, honest communication between stakeholders—clients, contractors, workers, and suppliers—is essential to navigating challenges and maintaining trust. The “Slack-like” communication hub on solutions like Bulk Exchange enhances communication but does not replace the human touch.
Successful construction projects require strong leadership to guide teams and resolve conflicts. Leaders must balance adopting technology with creating a culture of respect, inclusion, and collaboration.
Construction projects don’t just serve clients; they impact communities. Building trust with local stakeholders, addressing concerns, and maintaining transparency ensure long-term goodwill and project success.
Modernizing heavy civil construction doesn’t mean abandoning tradition. Instead, it’s about striking a balance where technology enhances human efforts rather than replacing them. Here’s how the industry can achieve this:
Equip workers with the skills to use modern tools effectively. Training programs that combine technical and interpersonal development will create well-rounded professionals capable of thriving in a tech-driven environment.
Adopting technology doesn’t have to happen overnight. Pilot programs and phased implementations allow teams to adapt gradually, ensuring a smoother transition.
Select tools that empower workers rather than replace them. For example, Bulk Exchange is set up to empower convenient communication and collaboration across industry stakeholders.
Recognize and honor the industry’s legacy by integrating modern practices with the interpersonal relationships that have always driven success.
Heavy civil construction is at a pivotal moment. The industry can address modern challenges by embracing technological solutions like Bulk Exchange while maintaining its commitment to human connection. This dual focus ensures that the sector remains efficient and innovative and grounded in the relationships that make it a vital part of society.
The path forward isn’t about choosing between technology and tradition but merging the two. Together, they will build the bridges, roads, and communities of tomorrow.
About the Author
Rachael Mahoney is the Chief Strategy Officer at Bulk Exchange. With extensive experience in the construction and technology sectors, she is passionate about driving innovation and fostering sustainable growth in the heavy civil construction industry. Follow Rachael for more insights on LinkedIn: Rachael Mahoney’s LinkedIn Profile.
Asphalt is a composite material made up of aggregates, binder, and filler. The binder serves as a glue to hold the aggregate particles together, creating a solid, durable surface.
In construction, few materials are as pivotal as asphalt. Known for its versatility, durability, and cost-effectiveness, asphalt plays a crucial role in building the infrastructure that connects our communities and powers our economies. But what exactly is asphalt used for in construction? Learn the many ways in which asphalt is utilized.
Asphalt is a composite material made up of aggregates, binder, and filler. The binder serves as a glue to hold the aggregate particles together, creating a solid, durable surface. Asphalt is known for its ability to withstand heavy loads and harsh weather conditions, making it an ideal choice for various construction projects from schools to the Indianapolis Motor Speedway.
There are several types of asphalt, each suited for different projects. Here are four of the main types of asphalt:
The benefits of using asphalt are numerous. It's cost-effective, easy to install, durable, and requires minimal maintenance. Asphalt is also recyclable, making it a sustainable choice for construction projects.
These parking lots require a durable, long-lasting surface to withstand constant use. Asphalt provides just that, offering a smooth, attractive finish that can endure heavy traffic and harsh weather conditions. Its quick installation time also means businesses can resume operations faster.
For residential driveways, asphalt offers a clean, aesthetically pleasing option. Its durability ensures it will last for years with minimal upkeep, and its flexibility allows it to adapt to ground movements, preventing cracks and potholes.
Industrial parking areas often see a lot of heavy machinery and vehicles. Asphalt can handle the weight and stress of industrial parking areas, providing a reliable and low-maintenance solution.
Airport runways need materials that can withstand extreme stress and varying weather conditions. Asphalt's flexibility allows it to accommodate the movements of large aircraft without cracking, ensuring a safe and smooth surface for taxiing planes.
Airport aprons, where planes are parked, loaded, and unloaded, require a strong surface. Asphalt's durability and low maintenance make it the best choice for airport aprons.
Pedestrian walkways constructed from asphalt provide a smooth, safe surface for walking. The material's flexibility allows it to adapt to ground movements, preventing cracks, ensuring durability
Bicycle paths benefit from asphalt's smooth surface by providing a comfortable ride for cyclists. The material's durability ensures the path can withstand constant use, while its low maintenance needs make it a cost-effective option for municipalities.
Recreational trails made from asphalt offer a reliable surface for walking, running, and biking. The material's ability to withstand various weather conditions and heavy use ensures that trails need minimal upkeep.
Industrial storage areas require a robust, durable surface to withstand heavy machinery and constant use. Asphalt provides just that, offering a low-maintenance, long-lasting solution for industrial environments.
Loading docks see constant use and heavy loads, requiring a strong, reliable surface. Asphalt's durability and flexibility make it an ideal choice for loading docks, ensuring a smooth, safe area for loading and unloading goods.
Manufacturing plants benefit from asphalt's properties, providing a durable, low-maintenance surface for heavy machinery and constant use. The material's flexibility allows it to adapt to ground movements, preventing cracks and damage.
From highways to airports to pedestrian walkways, asphalt plays a vital role in modern construction. Its versatility, durability, and sustainability make it an indispensable material for construction professionals and civil engineers. Understanding the various applications and benefits of asphalt can help you make informed decisions for your projects, ensuring long-lasting, high-quality results.
Don't let rework slow down your construction projects! Learn the top causes of rework and how to prevent them.
Construction projects are complex and they involve many moving parts, tight deadlines, and significant investments. However, one thing can derail even the most well-planned project—rework. Rework is estimated to represent between 2% and 20% of total costs, according to the Construction Industry Institute (CII). This financial burden can be overwhelming, especially for firms operating on thin margins. Find out the top causes of construction rework and how you can minimize it on your projects.
Effective scope and planning are the backbone of any construction project. Poor planning often results in insufficient resources, causing delays and necessitating rework. Scheduling mishaps can also lead to overlap in tasks, which creates confusion and errors.
A solid project plan should include detailed timelines, stakeholders, budget, resource allocation, and contingency plans. This ensures that everyone knows their role and responsibilities, reducing the likelihood of mistakes that lead to rework.
Communication is key in construction projects where numerous stakeholders are involved. A lack of clear communication can result in misunderstandings, incorrect implementations, and ultimately, rework. Regular meetings, status updates, and effective communication channels can mitigate this issue. Utilizing project management software can also streamline communication, ensuring that everyone is on the same page.
Accurate and up-to-date documentation is crucial for a smooth construction process. Incomplete or outdated documents can lead to errors in execution, requiring rework to correct. Ensure that all blueprints, plans, and permits are accurate and updated regularly. Implementing a robust document management system can help keep all documents organized and accessible.
Design changes are inevitable in construction, but they can be a significant cause of rework. To minimize this, establish a clear change management process. This should include evaluating the impact of changes, obtaining necessary approvals, and updating all relevant documents and plans accordingly.
Human error is one of the most common causes of rework in construction. Mistakes can happen at any stage, from planning to execution. Training and continuous education for all team members can help reduce human errors. Implementing checklists and quality control measures can catch mistakes before they escalate into rework.
Using poor materials can compromise the quality of work, necessitating rework to replace or repair the structure. Always source materials from reputable suppliers. Using poor materials can compromise the quality of work, necessitating rework to replace or repair the structure. It's crucial to have access to a variety of high-quality materials to match the specific needs of each project. Bulk Exchange offers an extensive selection of bulk materials from top-tier suppliers, giving you the variety and choice you need to select the right materials for your project. Additionally, our platform features detailed ratings and reviews, allowing you to make informed decisions based on the experiences of other professionals. This ensures you’re not only getting the best materials but also the most reliable suppliers, minimizing the risk of rework.
Construction projects must adhere to various standards and regulations. Failure to comply with these can result in rework to meet the required standards. Regular team training and audits can help maintain compliance.
Unpredictable weather conditions and other environmental factors can affect construction projects, causing delays and rework. While you can't control the weather, you can plan for it. Incorporate weather contingencies into your project plan and schedule tasks accordingly to minimize disruption.
Relying on subcontractors can introduce additional risks, including varying quality of work and adherence to schedules. Subcontractor issues can lead to rework if their work doesn't meet the project's standards. Vet subcontractors thoroughly before hiring; here are tips on how to vet subcontractors.
Using the wrong tools and equipment can lead to poor workmanship, resulting in rework to correct the issues. Make sure that all team members have access to the proper tools and equipment for their tasks. Regular maintenance and calibration of equipment can also help maintain quality.
Effective site management is crucial for a smooth construction process. Poor site management can result in disorganization, safety issues, and rework. Implementing a strong site management plan can help maintain order and efficiency as well as regular site inspections and safety checks can also help prevent issues that lead to rework.
Schedule regular meetings to ensure everyone is on the same page. Use these meetings to review progress, discuss potential issues, and clarify any concerns. Be sure to maintain detailed records of all project-related communications. This helps in mitigating misunderstandings and provides a reference point. Use any software that offers real-time communication and documentation sharing among project stakeholders.
Regularly update your team’s skills through training programs. Focus on both technical skills and soft skills like communication. Ensure that all team members have up-to-date safety training and understand the significance of following protocols because safety lapses can lead to rework.
Regular inspections and audits help identify potential issues before they become major problems and ensures that all work adheres to industry standards and codes. Consider hiring external experts for unbiased reviews of your processes and work quality.
Building Information Modeling (BIM) technology allows for comprehensive planning and visualization to manage schedules, track progress, and keep all team members informed, reducing the likelihood of errors. Construction management software apps allow for real-time updates and instant communication, making it easier to address issues as they arise.
Create detailed blueprints and project plans because the more thorough the plan, the fewer the chances for errors. Identifying potential risks at the outset and developing contingency plans is a proactive approach that can save time and money later on. Breaking a project into milestones and reviewing progress at each stage can also make it easier to catch and correct errors early.
Regularly updating clients on project progress and involving them in key decisions ensures that the final product meets their expectations.
Rework in construction is a costly and time-consuming issue, but it can be mitigated with the right process in place. By understanding the common causes and implementing preventive measures, this will help your projects run smoothly and efficiently. Streamline Your Next Project—Get Started with Bulk Exchange for Free!
Here are effective strategies for minimizing environmental impact in large civil construction projects. Find out how Bulk Exchange can help with your project.
With rapid urbanization and infrastructure development, the environmental impact of large civil construction projects has become a pressing issue. It’s more important than ever for industry professionals to implement sustainable practices. Learn ways to minimize your construction projects’ ecological footprint by using sustainable building materials.
Construction is a major driver of economic development, but it also poses significant environmental challenges. This sector is responsible for a substantial portion of global carbon emissions and waste production. Understanding these impacts is the first step in mitigating them effectively.
Two primary areas of concern are resource consumption and waste generation. Large construction projects often require vast amounts of materials like concrete, steel, and water, leading to resource depletion. Additionally, waste generated from construction sites contributes to landfill burdens and pollution.
The impact isn't limited to resource use and waste. Construction activities can disrupt local ecosystems, affect biodiversity, and cause air and water pollution. To address these issues, stakeholders must adopt a holistic approach, considering both the immediate and long-term environmental effects.
Navigating the complex landscape of environmental regulations is important to understand sustainable construction. International and local guidelines exist to ensure that construction practices minimize harm to the environment. Regulatory frameworks like the National Environmental Policy Act (NEPA) were enacted to ensure that federal agencies thoroughly consider the environmental impacts of their proposed actions before making decisions, requiring them to prioritize environmental factors alongside other considerations when planning projects. This was in response to growing public concern about the deteriorating quality of the environment and inadequate consideration of environmental impacts in major federal projects. Impact Statements (EISs) and Environmental Assessments (EAs) to assess the potential impacts of different courses of action.
In addition to legal requirements, numerous voluntary standards and certifications can guide construction projects. Certifications like Leadership in Energy and Environmental Design (LEED) encourage the adoption of sustainable practices by assessing various criteria such as energy efficiency, water use, and waste management.
Pre-Project EIA: Conduct comprehensive assessments to identify potential impacts on soil, water, air, and biodiversity. This analysis should inform the project’s design and decision-making.
One of the most exciting aspects of sustainable construction is the innovation in materials and technologies. Green materials are emerging as viable alternatives to traditional building materials, offering reduced environmental footprints and enhanced performance. For instance, green concrete is a sustainable alternative to traditional concrete that uses recycled materials and requires less energy to produce. Likewise, Cross-Laminated Timber (CLT) offers a renewable alternative to concrete and steel, providing structural integrity while storing carbon.
Technological advancements are also playing a crucial role in minimizing construction's environmental impact. Drones and sensors enable real-time monitoring of construction sites, improving efficiency and reducing waste. Meanwhile, Building Information Modeling (BIM) allows for precise planning and resource management, minimizing environmental impact.
Energy consumption during construction and operation phases is a significant contributor to environmental impact. To help reduce your carbon footprint, construction companies can adopt strategies like prefabrication which reduces energy use by assembling components off-site in controlled environments. This not only minimizes energy consumption, but also decreases waste and transportation emissions.
Incorporating renewable energy sources like solar panels and wind turbines into construction sites can further help with energy efficiency. These technologies provide clean energy to power construction activities, reducing reliance on fossil fuels.
Construction projects can strain local water supplies if not managed carefully, so efficient water management strategies are essential for sustainable construction. Some water management strategies for construction include: rainwater harvesting, greywater recycling, using water-saving fixtures like low-flow taps and dual-flush toilets, implementing smart irrigation systems, and proper soil management.
Waste management is a key aspect of sustainable construction. By minimizing waste generation and promoting recycling, construction projects can significantly reduce their environmental impact. On-site waste separation is a good strategy for managing waste efficiently. By sorting materials like wood, metal, and concrete, construction companies can divert waste from landfills and send it to recycling facilities. Construction waste can also be repurposed into new building materials, reducing the need for more resources.
The field of sustainable construction is constantly evolving, driven by technological advancements and changing consumer expectations. Staying informed about future trends will help you remain competitive and environmentally responsible.
Some of other emerging trends include:
It’s important to continuously monitor and audit the environmental impact your construction project has. Use air quality monitors, noise sensors, and water quality testers to track the environmental impact in real time. Implement systems Environmental Management Systems (EMS) like ISO 14001 to streamline environmental management processes and ensure compliance. Make sustainable building choices in an effort to help keep the environment clean.
Are you starting a construction project and need to find the right material? We can help you source the material you’ll need for your project and have also added a carbon calculator feature so you can make the right financial and environmental choice for your project. Get started with Bulk Exchange for free today!
Ahhh, St. Patrick’s Week, the one time of year when everyone suddenly discovers their long-lost Irish granny, and Guinness sales mysteriously triple. It’s a grand time altogether, with parades, pints, and questionable attempts at an Irish accent. But beyond the shamrocks and shenanigans, it’s worth remembering the deeper legacy of the Irish in America, one not just built on celebrations, but on sheer grit, resilience, and the ability to build things that last.
As a proud Irish American with deep roots in both tech and construction, I don’t just celebrate my heritage, I walk on it, work with it, and build upon it every day. The Irish didn’t just show up for the craic (though let’s be honest, we do love a good party). When Irish immigrants landed on these shores, they got straight to work, designing and constructing the backbone of this country. From the White House to the Golden Gate Bridge, from tunnels to towering skyscrapers, the Irish left their mark. Not with riches or privilege, but with sheer determination, strong backs, and the unshakable belief that they could build something better in their chosen home and country.
Fast forward a century or two, and the Irish are still at it. Instead of just building roads and bridges, we’re laying the foundation for the digital world. Paul Foley, my own CEO at Bulk Exchange and a proud son of County Leitrim, is part of that new wave, building the construction tech infrastructure that powers our modern economy. And let’s not forget the Collison brothers, two lads from rural Ireland who founded Stripe and reshaped online payments globally. Whether it’s steel and concrete or code and connectivity, the Irish spirit of resilience and innovation hasn’t changed and we’re still getting the job done.
Why are the Irish so good at this? Maybe it’s because we’ve always known how to push forward, no matter the odds. Whether it was swinging hammers or writing lines of code, the same qualities that built America’s physical landscape are now shaping its digital future: toughness, adaptability, and an innate ability to solve problems (usually with a bit of charm thrown in for good measure).
So this week, when you raise a glass at the parade, take a moment to remember, there’s a good chance the road you traveled to get there, and the tech you used to plan or pay for your night out, have the Irish to thank. Sláinte to the builders, past, present, and future!
About the Author
Rachael Mahoney is the Chief Strategy Officer at Bulk Exchange. With extensive experience in the construction and technology sectors, she is passionate about driving innovation and fostering sustainable growth in the heavy civil construction industry. Follow Rachael on LinkedIn for more insights.
In construction, few materials are as pivotal as asphalt. Known for its versatility, durability, and cost-effectiveness, asphalt plays a crucial role in building the infrastructure that connects our communities and powers our economies. But what exactly is asphalt used for in construction? Learn the many ways in which asphalt is utilized.
Asphalt is a composite material made up of aggregates, binder, and filler. The binder serves as a glue to hold the aggregate particles together, creating a solid, durable surface. Asphalt is known for its ability to withstand heavy loads and harsh weather conditions, making it an ideal choice for various construction projects from schools to the Indianapolis Motor Speedway.
There are several types of asphalt, each suited for different projects. Here are four of the main types of asphalt:
The benefits of using asphalt are numerous. It's cost-effective, easy to install, durable, and requires minimal maintenance. Asphalt is also recyclable, making it a sustainable choice for construction projects.
These parking lots require a durable, long-lasting surface to withstand constant use. Asphalt provides just that, offering a smooth, attractive finish that can endure heavy traffic and harsh weather conditions. Its quick installation time also means businesses can resume operations faster.
For residential driveways, asphalt offers a clean, aesthetically pleasing option. Its durability ensures it will last for years with minimal upkeep, and its flexibility allows it to adapt to ground movements, preventing cracks and potholes.
Industrial parking areas often see a lot of heavy machinery and vehicles. Asphalt can handle the weight and stress of industrial parking areas, providing a reliable and low-maintenance solution.
Airport runways need materials that can withstand extreme stress and varying weather conditions. Asphalt's flexibility allows it to accommodate the movements of large aircraft without cracking, ensuring a safe and smooth surface for taxiing planes.
Airport aprons, where planes are parked, loaded, and unloaded, require a strong surface. Asphalt's durability and low maintenance make it the best choice for airport aprons.
Pedestrian walkways constructed from asphalt provide a smooth, safe surface for walking. The material's flexibility allows it to adapt to ground movements, preventing cracks, ensuring durability
Bicycle paths benefit from asphalt's smooth surface by providing a comfortable ride for cyclists. The material's durability ensures the path can withstand constant use, while its low maintenance needs make it a cost-effective option for municipalities.
Recreational trails made from asphalt offer a reliable surface for walking, running, and biking. The material's ability to withstand various weather conditions and heavy use ensures that trails need minimal upkeep.
Industrial storage areas require a robust, durable surface to withstand heavy machinery and constant use. Asphalt provides just that, offering a low-maintenance, long-lasting solution for industrial environments.
Loading docks see constant use and heavy loads, requiring a strong, reliable surface. Asphalt's durability and flexibility make it an ideal choice for loading docks, ensuring a smooth, safe area for loading and unloading goods.
Manufacturing plants benefit from asphalt's properties, providing a durable, low-maintenance surface for heavy machinery and constant use. The material's flexibility allows it to adapt to ground movements, preventing cracks and damage.
From highways to airports to pedestrian walkways, asphalt plays a vital role in modern construction. Its versatility, durability, and sustainability make it an indispensable material for construction professionals and civil engineers. Understanding the various applications and benefits of asphalt can help you make informed decisions for your projects, ensuring long-lasting, high-quality results.
Reducing waste in construction is crucial for several reasons including, environmental sustainability, cost efficiency, and resource conservation. With the goal of creating a more sustainable environment, it’s important to understand why reducing material waste in construction projects is essential. Find out how to reduce material waste in this blog.
Construction waste can include a wide range of materials such as concrete, bricks, wood, metal, insulation, and glass. It often results from excess materials ordered, off-cuts, or materials damaged during construction activities.
Waste management in construction is a challenge that the industry has been grappling with for years. Without proper planning and conscious effort, construction sites can produce vast amounts of waste that contribute to landfill overflow and environmental pollution.
Proper waste management can significantly reduce the amount of waste that ends up in landfills, reducing the industry's carbon footprint and conserving natural resources by recycling and reusing materials.
Reducing waste can lead to substantial cost savings. By estimating the amount of materials you’ll need and reusing and recycling where possible, construction companies can reduce purchase costs and disposal fees.
Many regions have strict regulations regarding waste disposal and recycling. Learn more about the federal environmental requirements for construction here.
Demonstrating a commitment to reducing waste can enhance your brand and attract more eco-conscious customers.
A waste management plan for a construction project is a blueprint for how materials will be managed on-site. It should detail the types of waste expected, how it will be handled, and the disposal or recycling methods.
Ordering the correct amount of materials and handling them properly can greatly reduce waste. Use just-in-time delivery systems to prevent material spoilage on-site and plan for material storage to protect them from damage.
Design plays a critical role in waste management. Designing buildings and infrastructures with precise measurements can prevent the over-ordering of materials.
Whenever possible, choose deconstruction over demolition. Deconstruction allows for the careful dismantling of buildings to salvage materials for reuse or recycling, rather than demolishing them and sending the materials to a landfill.
To make a construction waste management plan effective, here are some ideas on how to implement it.
Train your workforce on the importance of waste management and how they can contribute to reducing waste. Awareness is key to ensuring that everyone follows the waste management plan.
On-site segregation of waste materials is essential. Provide different bins for various types of waste and ensure they are clearly labeled. This makes recycling and disposal more manageable and more efficient.
Regularly monitor waste levels and report on waste management outcomes. This will help identify areas for improvement and ensure the waste management plan is being followed.
Lean construction encourages continuous improvement through regular reviews and updates of waste management practices. Learn from each project and refine your strategies accordingly.
Despite the clear benefits, there are challenges in reducing waste in construction. These include:
A lack of knowledge or expertise in waste management can hinder the implementation of effective strategies.
Sometimes the upfront costs of waste management practices such as purchasing recycling equipment can be a deterrent.
The logistics of dividing, storing, and transporting waste for recycling can be complex, especially on constrained sites.
With continued innovation and commitment, the construction industry can minimize its environmental impact, save costs, and contribute to a more sustainable future.
Today, environmental consciousness is more crucial than ever with sustainable construction at the forefront of this conversation. Sustainable construction is also referred to as green design where every aspect of building, from design to demolition is eco-friendly and resource-efficient. Sustainability is not just a buzzword, it’s a shift in how we think about the places we live, work, and play. For contractors, architects, and homeowners, understanding sustainable building construction will help you make eco-friendly choices for your next project.
Sustainable building construction refers to creating structures using processes that are environmentally responsible and resource-efficient throughout a building’s life cycle. This includes everything from the initial design to construction, operation, maintenance, and demolition. The goal is to minimize the environmental impact and create buildings that are energy-efficient, healthy for occupants, and economically viable.
To build with sustainability in mind, these principles need to be taken into consideration:
Sustainable building construction offers numerous environmental benefits that make it a critical practice for our future.
New Buildings Institute states that “buildings account for 39% of global energy-related carbon emissions worldwide: 28% from operational emissions (from energy needed to heat, cool and power them), and the remaining 11% from materials and construction.” Sustainable construction can drastically reduce these emissions by using energy-efficient designs and renewable energy sources like solar or wind power. Every effort to cut down on energy consumption is important.
Traditional construction methods use vast amounts of natural resources including water, wood, and minerals. Sustainable practices focus on conserving these resources by using recycled materials, implementing water-saving technologies, and choosing sustainable materials that are abundant and renewable.
Construction can often lead to habitat destruction and loss of biodiversity. By adopting sustainable practices, we can minimize land disruption and protect natural habitats. Green roofs and walls for instance, can provide a sanctuary for local wildlife even in urban areas.
Sustainable building isn’t just good for the planet, it’s also smart for business. Here’s some ways it helps businesses:
Innovation is at the heart of sustainable construction. Here are some technologies making shaping the industry:
Ready to start incorporating sustainable practices in your construction business? Here are some things to consider:
Emerging technologies and growing awareness is driving the construction industry towards more sustainable practices. Learn more about the future of construction technology advancements and how it can help you grow your business by implementing sustainable operations and materials.
In the world of construction where deadlines are tight and margins can be thin, efficiency is key to running your business. Yet, many construction companies still rely on paperwork to manage projects. Transitioning to a digital project management solution can streamline operations and reduce overhead. Learn more about the benefits of a paperless system so you can move towards a more efficient construction business.
Switching your business to a paperless system means replacing physical documents with cloud-based software solutions for everything from blueprints to contracts. By adopting these technologies, construction businesses can save time, reduce costs, and streamline processes.
Paper-based systems are often cumbersome and time-consuming. Digital tools allow for quicker access to information, seamless communication, and real-time updates. This means less time spent searching for documents and more time focusing on the project.
Printing, storing, and managing paper documents can be expensive. By going paperless, construction companies can significantly cut down on these costs.
Keeping up with compliance and reporting requirements can be complex. Digital tools can streamline this process by automating compliance checks and generating reports. This ensures that your company meets all regulatory requirements without extra effort.
Eco-conscious businesses recognize the importance of reducing their carbon footprint. Going paperless is a significant step towards sustainability, as it minimizes the use of paper and reduces waste. This not only benefits the environment but also enhances the company's reputation as a green business.
Cloud-based solutions enable team members to collaborate from different locations. Whether working on-site or remotely, everyone can access the same information and contribute to the project in real-time. This leads to better teamwork and more efficient project management.
By switching to cloud-based software for construction projects, team members can access important documents on their phones or tablets which means that even when they're on a site, they can review plans, update progress, and communicate with the team.
The first step in going paperless is selecting the right software. Look for solutions that offer project management, reporting, system integration, storage, mobile compatibility, and collaboration features.
Transitioning to a paperless system requires training, so it’s important to ensure your team has the right training so they feel confident using the software.
Finding specific documents in a mound of paperwork can be challenging. Cloud storage solutions offer easy retrieval through search functions, tags, and organized folders⎯this will save a lot of time.
Security is a concern for construction companies. Cloud solutions offer secure storage with encryption and access controls. This ensures that sensitive information is protected from unauthorized access.
A report on LinkedIn states that “an estimated $273 billion worth of construction errors made each year in the U.S. alone, which leads many construction firms to bake rework into the cost of construction, creating a contingency budget.” This is where cloud-based software comes in because it can automate workflows, such as approvals and notifications, to reduce delays caused by manual processes.
Going paperless is a significant step toward modernizing your company and staying competitive in the construction industry. There will be an initial investment in the technology and training of your team, but the long-term advantages make it advantageous to adopt a paperless company.